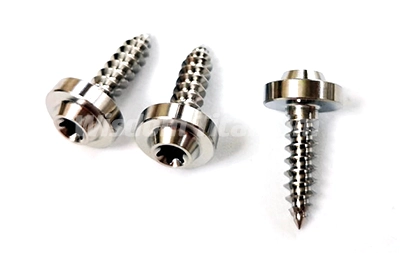
I recognize the necessity of picking the right substances and screws for various tasks as an engineer with numerous years of knowledge in the field of engineering. Titanium self-tapping screws are distinctive among the various possibilities that exist for multiple reasons, which lend them a fantastic option. I am going to discuss the special characteristics, functions, and benefits of titanium self-tapping screws in this post, as well as the scientific basis for their preference over other types of screws.
Why Are Titanium Self-Tapping Screws the Preferred Choice in Diverse Industries?
The noteworthy strength-to-weight ratio of titanium screws means that self-tapping is one of the clearest justifications for the idea of utilizing them. Titanium has been praised for possessing a staggering strength that is only slightly lighter in weight than iron. Due to this unique value, titanium screws are capable of handling far greater amounts of abuse than steel screws while remaining of identical durability. Titanium screws are especially beneficial in industries where weight reduction is critical, including in the aerospace, automotive, and nautical sectors, owing to this property.
Titanium's superior toughness also makes it feasible to create self-tapping screws with more detailed tolerances. The anchors' capacity to hold surfaces better and tolerate outside forces or tremors is facilitated by the finer needles. For consumption in mechanical gatherings, mobile devices, and even surgical implants, titanium self-tapping screws tend to be suitable.
Titanium screw heads deliver remarkable shielding against corrosion aside from their strong construction and tiny weight. Even in highly damaging media like ocean water, acids, and bases, titanium exhibits unusual resistance to corrosion, in contrast to metal, which is susceptible to pitting and rusting when handled with moisture or harsh surroundings. This inherent corrosion resistance makes titanium self-tapping screws suitable for use in outdoor applications, marine environments, and chemical processing plants.
Furthermore, titanium self-tapping screws are biocompatible, making them ideal for use in medical implants and surgical procedures. Their corrosion resistance and longevity ensure the integrity and functionality of implants over extended periods, reducing the risk of complications and the need for revision surgeries.
Overall, the superior strength, lightweight nature, corrosion resistance, and biocompatibility of titanium self-tapping screws make them a preferred choice for engineers and manufacturers worldwide. These screws offer exceptional performance and reliability in a wide range of applications, from demanding industrial settings to delicate medical procedures.
Why Are Titanium Self-Tapping Bolts Unmatched for Corrosion Resistance and Longevity?
Excellent durability against oxidation is another notable aspect of titanium self-tapping bolts. Even in highly destructive mediums like water from the sea, chemicals, and alkaline solutions, titanium exhibits unusual resistance to rusting, in contrast to steel, which is at risk of rust and corrosion when faced with moisture or adverse conditions. The development of a fragile, stable oxide coating on titanium's exterior is to blame for its intrinsic immunity to weathering. Like the coating of passivation on stainless steel's surface, this oxide layer acts like insulation to avoid rust.
Because titanium is impervious to deterioration, it is an excellent material to utilize in settings where being around humidity or aggressive substances is inescapable. These applications include outdoor construction, marine structures, chemical processing plants, and even biomedical implants. The exceptional longevity of titanium self-tapping screws ensures reliable performance and maintenance-free operation over extended periods. This reduces the need for frequent replacements and associated downtime, leading to increased efficiency and reduced maintenance costs.
In addition to their corrosion resistance, titanium self-tapping screws also offer excellent resistance to wear and abrasion. This makes them suitable for use in demanding applications where screws are subjected to high levels of friction and wear, such as in industrial machinery, automotive components, and aerospace systems. The combination of corrosion resistance, longevity, and wear resistance makes titanium self-tapping screws an excellent choice for applications requiring reliable and durable fastening solutions.
Furthermore, titanium self-tapping screws are biocompatible, making them suitable for use in medical implants and surgical procedures. Their corrosion resistance and longevity ensure the integrity and functionality of implants over extended periods, reducing the risk of complications and the need for revision surgeries.
Overall, the corrosion resistance and exceptional longevity of titanium self-tapping screws make them a preferred choice for applications where reliability, durability, and long-term performance are critical.
Why is Titanium the Material of Choice for Medical Implants and Surgical Instruments?
Titanium is an appropriate substance for use in healthcare and scientific uses due to its particular physiological amenities, which go beyond its strength and capacity for corrosion. Since titanium is natively compatible with life, the human body may embrace it, and it is unlikely to respond unfavorably or generate an immune system reaction when transplanted into or in contact with tissues throughout the body. Considering titanium is compatible and is capable of creating an intense connection with living bone organs, it is frequently employed in dental and orthopedic surgical implants as well as surgical instruments.
When it comes to self-tapping screws, titanium is the substance preferred for surgical devices and medical supplies where long-term biostability and friendliness are crucial since it has the ability to adapt and resistance to corrosion. Whether used in orthopedic fixation plates, spinal implants, or dental prosthetics, titanium self-tapping screws offer surgeons and patients alike the assurance of reliable performance, reduced risk of complications, and improved patient outcomes.
Conclusion
In conclusion, the decision to choose titanium self-tapping screws is grounded in their unparalleled combination of strength, lightweight nature, corrosion resistance, and biocompatibility. These screws offer superior performance and longevity across a diverse range of applications, from aerospace and automotive engineering to marine construction and medical implantology. By harnessing the unique properties of titanium, engineers and manufacturers can achieve optimal results, ensuring the reliability, durability, and safety of their products.
If you want to know more about Titanium Self-Tapping Screws, please contact us: sales@wisdomtitanium.com.
References
-
ASTM International. (2019). Standard Specification for Titanium and Titanium Alloy Wire. ASTM B863/B863M-19.
-
Boyer, R. R. (2006). An overview on the use of titanium in the aerospace industry. Materials Science and Engineering: A, 213(1-2), 103-114.
- Geetha, M., Singh, A. K., Asokamani, R., & Gogia, A. K. (2009). Ti based biomaterials, the ultimate choice for orthopaedic implants–A review. Progress in materials science, 54(3), 397-425.