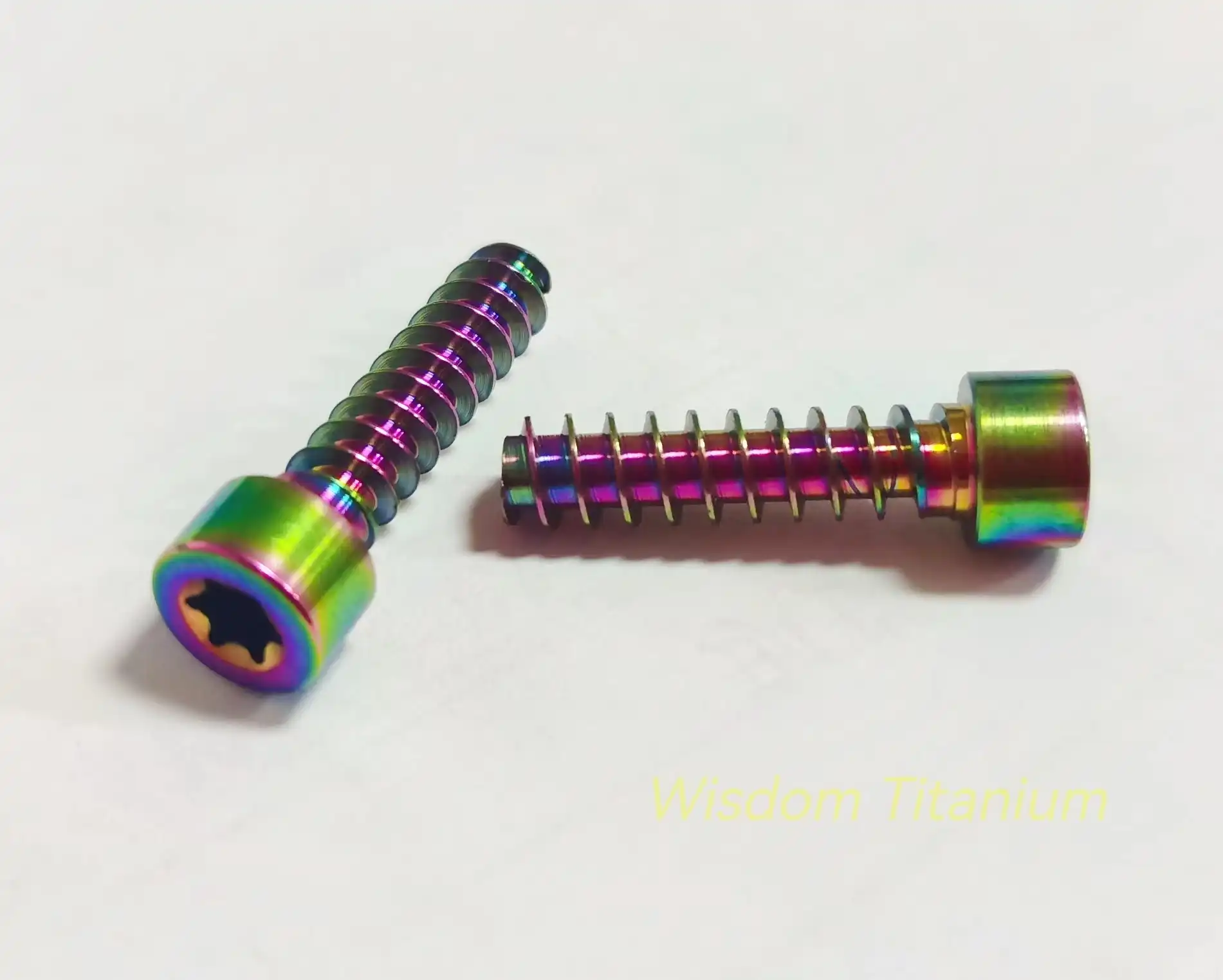
I am constantly captivated by the extraordinary qualities of titanium screw, particularly their unparalleled resistance to corrosion and abrasion, as I am deeply immersed in materials science and engineering. I want to explain why titanium screws are becoming a popular choice in a variety of industrial contexts by looking at the scientific foundations that support this unique feature. Digging into the perplexing subtleties of titanium's sub-atomic design and surface properties, we unwind the mysteries behind its noteworthy strength and life span in testing conditions. By taking apart the components that empower titanium screws to oppose consumption and wear, we gain a significant comprehension of their predominance and dependability in different modern applications. This investigation not only demonstrates the distinctive advantages of titanium screw but also the central role they play in ensuring optimal performance and durability in a variety of industrial fields.
Titanium screw is a conspicuous progress metal that is broadly utilized in various areas, including the aviation, clinical, car, and marine areas, because of its momentous solidarity to-weight proportion and consumption opposition. In the domain of attaching arrangements like screws, titanium's particular attributes present significant advantages contrasted with regular materials like steel or aluminum. Its excellent properties add to upgraded execution as well as guarantee life span and unwavering quality in different applications. The widespread use of titanium fasteners demonstrates its superiority in crucial industries where weight and durability are of the utmost importance. Manufacturers are able to improve the efficiency and safety of complex systems by optimizing the design and functionality of components by making use of titanium's distinctive properties. This persevering through allure of titanium as a favored material for latches features its flexibility and versatility in satisfying the severe needs of current modern practices.
Can Titanium Screws Provide Superior Corrosion and Wear Resistance?
The importance of corrosion resistance cannot be overstated when considering the functionality and lifespan of screws, particularly in environments characterized by high levels of moisture, chemical exposure, or salt presence. Titanium's exceptional resistance to corrosion is rooted in its innate capacity to develop a protective oxide film on its surface upon interaction with oxygen. This oxide film, predominantly comprising titanium dioxide (TiO2), serves as a formidable shield, effectively obstructing additional oxidation and corrosion of the underlying titanium material. By forming a robust barrier through the oxide layer, titanium effectively thwarts the detrimental effects of corrosive agents, thereby ensuring the structural integrity and longevity of screws in challenging operating conditions. This fundamental mechanism highlights titanium's prowess in withstanding corrosive environments and underscores its significance as a preferred choice for applications demanding superior corrosion resistance and durability.
Titanium's oxide layer, as opposed to steel, which is helpless to rust and weakening within the sight of dampness and oxygen, is very steady much under the most outrageous circumstances. This outstanding resilience can be credited to the robust bond between titanium atoms and oxygen atoms, culminating in the formation of a dense and firmly attached oxide layer. As a result, this oxide layer serves as a highly effective shield, safeguarding the underlying titanium metal from the damaging impact of corrosive elements. The enduring stability of this oxide layer underscores titanium's unparalleled resistance to corrosion, positioning it as a highly reliable and durable material in environments where protection against degradation is vital. By virtue of its inherent capability to maintain structural integrity in the face of harsh external factors, titanium emerges as an indispensable choice for applications necessitating uncompromising corrosion resistance and long-term performance.
Beyond its passive defense mechanism of oxide layer formation, titanium showcases active corrosion resistance by possessing the unique capability to autonomously repair compromised oxide layers when subjected to scratches or abrasion. This inherent self-healing attribute plays a pivotal role in enhancing the long-term durability and dependability of titanium in demanding environments characterized by significant mechanical stress and wear. The ability of titanium to spontaneously mend damaged oxide layers underscores its resilience against corrosion-induced degradation, reinforcing its reputation as a top-tier material for applications requiring steadfast performance and robust protection against environmental challenges. By seamlessly addressing surface imperfections and restoring protective barriers, titanium exemplifies a proactive approach to corrosion resistance, ensuring sustained functionality and structural integrity over extended periods of use. This remarkable self-repairing feature further solidifies titanium's position as a premier choice for critical applications where reliability and longevity are paramount considerations.
Apart from their impressive corrosion resistance, titanium screw are distinguished by their outstanding wear resistance, rendering them well-suited for applications exposed to substantial friction and mechanical strain. The superior wear resistance of titanium screws can be attributed to their elevated hardness and low friction coefficient, characteristics that effectively mitigate surface degradation and minimize friction-induced losses. By virtue of these inherent properties, titanium screws exhibit remarkable durability and longevity in scenarios where the risk of wear and tear is pronounced. The combination of high hardness and reduced friction not only enhances the overall performance of titanium screws but also ensures reliable functionality in high-stress environments. This exceptional wear resistance underscores the suitability of titanium screws for critical applications demanding resilience against abrasive forces, affirming their status as a preferred choice for industries requiring robust fastening solutions with enduring performance capabilities.
Can Titanium's Hardness and Low Friction Coefficient Enhance Performance in High-Stress Environments?
The remarkable hardness of titanium, akin to that of steel, plays a pivotal role in preserving its surface integrity and shielding it from deformation, particularly in situations characterized by elevated stress levels. This notable hardness primarily emanates from the hexagonal close-packed (HCP) crystal structure inherent in titanium, which confers exceptional strength and rigidity upon the material. The presence of this crystal structure fortifies titanium, enabling it to maintain its structural form and resist deformation even when subjected to rigorous conditions. By leveraging its robust HCP crystal arrangement, titanium effectively upholds its surface integrity, safeguarding against detrimental impacts and ensuring sustained performance in demanding operational environments. This inherent hardness, underpinned by the unique crystal structure, underscores titanium's capacity to endure high-stress scenarios while preserving its structural soundness, thereby solidifying its standing as a reliable and resilient material for applications necessitating unwavering durability and resistance to deformation.
Additionally, titanium's advantageous low friction coefficient mitigates the prevalent problems of galling and seizing often associated with conventional metal fasteners. This attribute is attributable to the smooth surface finish of titanium and the lubricating impact of its protective oxide layer, both of which contribute to the reduction of frictional forces and the optimization of mechanical system performance. The combination of a polished surface and the presence of the oxide layer ensures that titanium fasteners experience minimal resistance when in use, effectively minimizing the occurrence of galling and seizing, which are common challenges encountered with other metal fasteners. By virtue of its reduced friction coefficient, titanium not only enhances the operational efficiency of mechanical systems but also diminishes the likelihood of detrimental issues such as galling and seizing, thereby positioning itself as a reliable and preferred choice for applications requiring dependable and friction-averse fastening solutions.
Conclusion
In rundown, the outstanding consumption and wear opposition of titanium screw can be credited to a mix of elements, including the development of a defensive oxide layer, dynamic erosion obstruction, high hardness, and low rubbing coefficient. These properties make titanium screws profoundly alluring for a large number of utilizations where sturdiness, unwavering quality, and execution are principal. The unique properties of titanium make it an ideal choice for demanding applications where corrosion and wear resistance are critical factors. By understanding the scientific basis behind titanium's exceptional performance, engineers and manufacturers can make informed decisions when selecting fasteners for their projects.
If you want to learn more about titanium screws, welcome to contact us: sales@wisdomtitanium.com.
References
Moustafa, E. S., Ataya, S., El-Tayeb, T. A., & Maksoud, H. A. (2018). Mechanical and tribological properties of Ti-6Al-4V and Ti-6Al-7Nb biomedical alloys. Tribology International, 123, 142-149.
Raghavendra, N., & Anilchandra, S. M. (2007). Corrosion of titanium dental implants. The Journal of Indian Prosthodontic Society, 7(2), 80.
Joska, L., & Vlček, M. (2010). Effective corrosion protection of titanium by plasma electrolytic oxidation. Electrochimica Acta, 55(23), 6959-6967.
White, S. E., & Mayville, R. W. (1997). The Friction and Wear of Titanium in Various Environments. Tribology Transactions, 40(4), 650-656.
Jones, D. A., & Feilden, E. (2000). The influence of surface treatment on the wear and corrosion behaviour of titanium. Wear, 246(1-2), 156-164.
Niinomi, M. (2003). Recent metallic materials for biomedical applications. Metallurgical and Materials Transactions A, 35(3), 691-700.