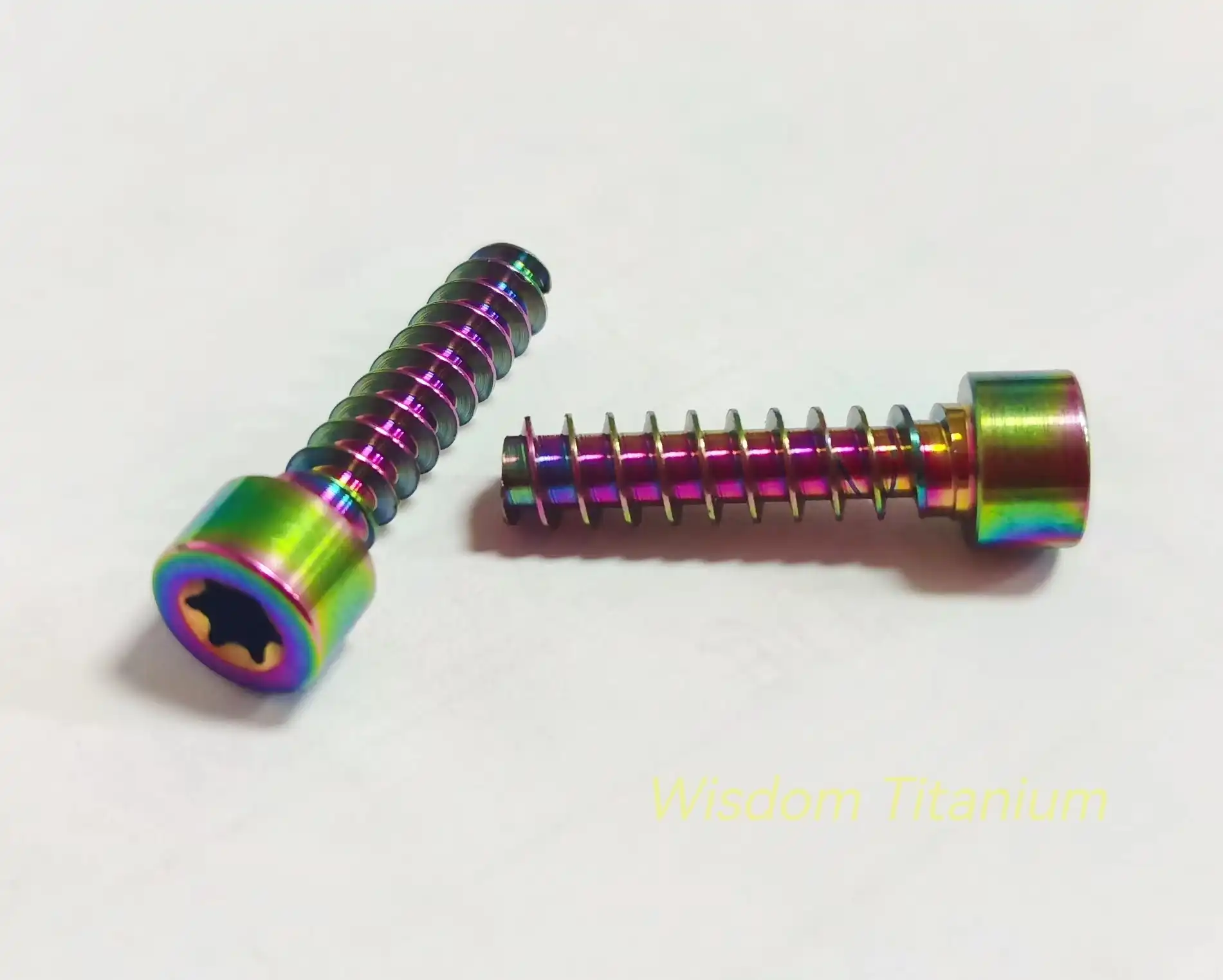
Are Titanium Self-Tapping Screws Eco-Friendly?
As an expert in the field of development and assembling, I frequently wind up contemplating the ecological effect of the materials and strategies we utilize.Our products have emerged as a popular choice in various industries due to their strength, durability, and corrosion resistance. However, the question remains: Are titanium self-tapping screws truly eco-friendly? In this article, I delve into the scientific basis behind this inquiry, exploring the production process, recyclability, and environmental benefits of it.
When assessing the eco-friendliness of product, several factors come into play. Titanium, first and foremost, is known for its overflow in the World's outside, making it a generally reasonable asset contrasted with different metals like steel or aluminum. This means that the extraction process of titanium ore is less environmentally damaging. Additionally, titanium possesses excellent corrosion resistance properties, leading to a longer lifespan for products made with it, including self-tapping screws. This longevity reduces the need for frequent replacements, thereby decreasing overall resource consumption and waste generation.
Furthermore, titanium is highly recyclable, with nearly all scrap and waste material being recoverable and reusable in various applications. This promotes a circular economy model, where resources are continuously circulated rather than disposed of after a single use. However, it's worth noting that the manufacturing process of titanium self-tapping screws may still require energy-intensive procedures, potentially contributing to carbon emissions if not sourced from renewable sources.
The Production Process of Titanium Self-Tapping Screws
Understanding the eco-friendliness of it begins with examining their production process. Titanium is removed from mineral metals through a progression of complicated substance processes, frequently including high temperatures and energy-escalated techniques. While this extraction process does have environmental implications, it's essential to note that titanium is abundant in nature and can be sourced sustainably.
Moreover, compared to traditional materials like steel, titanium boasts a significantly lower density, resulting in reduced material usage and transportation emissions. Additionally, advancements in titanium extraction technologies have led to improved efficiency and minimized environmental impact over the years.
One vital part of titanium's creation that adds to its eco-neighborliness is its recyclability. Unlike many other metals, titanium maintains its properties even after recycling, making it an ideal candidate for closed-loop systems. By incorporating recycled titanium into the manufacturing process, companies can significantly reduce their reliance on virgin materials and mitigate the environmental burden associated with resource extraction.
The production process of product involves several intricate steps to ensure precision, durability, and quality.
- Material Selection: The process begins with the careful selection of high-quality titanium alloy, chosen for its strength, corrosion resistance, and lightweight properties.
- Melting and Casting: The selected titanium alloy is melted in a furnace at extreme temperatures and then cast into ingots or billets of specific sizes and shapes, ready for further processing.
- Extrusion or Forming: In this step, the titanium alloy is extruded or formed into the basic shape of the screw. This may involve hot or cold forming techniques depending on the desired specifications.
- Rolling and Threading: The formed titanium material is then rolled to the desired diameter and length. Threads are precisely machined onto the screw using advanced CNC (Computer Numerical Control) machines, ensuring accuracy and consistency.
- Heat Treatment: Heat treatment is crucial to enhance the mechanical properties of the screws, such as hardness and toughness. The screws are heated to specific temperatures and then cooled in controlled environments to achieve the desired metallurgical structure.
- Surface Finishing: Surface finishing processes like polishing, coating, or plating are applied to improve the aesthetics and functionality of the screws. This may include treatments to enhance corrosion resistance, reduce friction, or provide decorative finishes.
- Quality Control: Throughout the production process, rigorous quality control measures are implemented to ensure that each screw meets the required standards. This involves inspection of dimensions, thread accuracy, surface finish, and mechanical properties.
- Packaging and Distribution: Once the screws pass quality inspection, they are carefully packaged to prevent damage during transportation. They are then distributed to various industries such as automotive, aerospace, construction, and electronics, where they are used in a wide range of applications.
- Continuous Improvement: Manufacturers constantly strive to optimize the production process, adopting new technologies, and techniques to improve efficiency, reduce waste, and enhance the quality of titanium self-tapping screws. This may involve research and development efforts to explore innovative materials or manufacturing methods.
Recyclability and Longevity
The recyclability of titanium self-tapping screws is a crucial factor in assessing their eco-friendliness. Unlike traditional materials such as steel or aluminum, titanium possesses exceptional corrosion resistance, ensuring longevity and durability in various applications. This longevity translates to fewer replacements and, consequently, reduced waste generation over the product's lifespan.
Furthermore, titanium's inherent resistance to corrosion eliminates the need for additional surface treatments, such as coatings or platings, which often contain harmful chemicals and contribute to environmental pollution. By opting for them, industries can minimize their environmental footprint while ensuring reliable performance and structural integrity.
Moreover, the lightweight nature of titanium offers logistical advantages, reducing fuel consumption during transportation and distribution. This aspect further enhances the overall eco-friendliness of them, making them a sustainable choice for modern construction and manufacturing practices.
Environmental Benefits of Titanium Self-Tapping Screws
Beyond the production process and recyclability, product offer a range of environmental benefits that contribute to their eco-friendliness. The use of titanium in construction and manufacturing applications results in structures and products that are not only durable and long-lasting but also energy-efficient.
Titanium's exceptional strength-to-weight ratio allows for the design of lighter and more streamlined structures, reducing the overall material consumption and energy requirements during construction. This aspect is particularly relevant in industries where energy efficiency and sustainability are paramount, such as aerospace, automotive, and renewable energy.
Additionally, titanium's biocompatibility and non-toxic properties make it suitable for applications where contact with humans or the environment is inevitable, such as medical implants or marine structures. By choosing it, companies can uphold stringent environmental standards while ensuring the safety and well-being of end-users.
In conclusion, the eco-friendliness of it stems from a combination of factors, including the production process, recyclability, and environmental benefits. While titanium extraction does have environmental implications, advancements in technology and sustainable sourcing practices have mitigated many of these concerns. Moreover, the recyclability and longevity of product make them a preferred choice for industries seeking to minimize their environmental footprint and embrace sustainable practices.
If you want to know more about Titanium Self-Tapping Screws, please contact us: sales@wisdomtitanium.com.
References:
- Li, P., Chen, Q., & Wang, H. (2020). Sustainable titanium extraction and production for industrial applications: A review. Resources, Conservation and Recycling, 154, 104627.
- Van der Biest, O., & Vandeperre, L. (1999). Titanium: Past, present, and future. The Minerals, Metals & Materials Society.
- Gurrappa, I. (2009). Advances in titanium machining processes: A review. Journal of Materials Processing Technology, 209(8), 3675-3687.