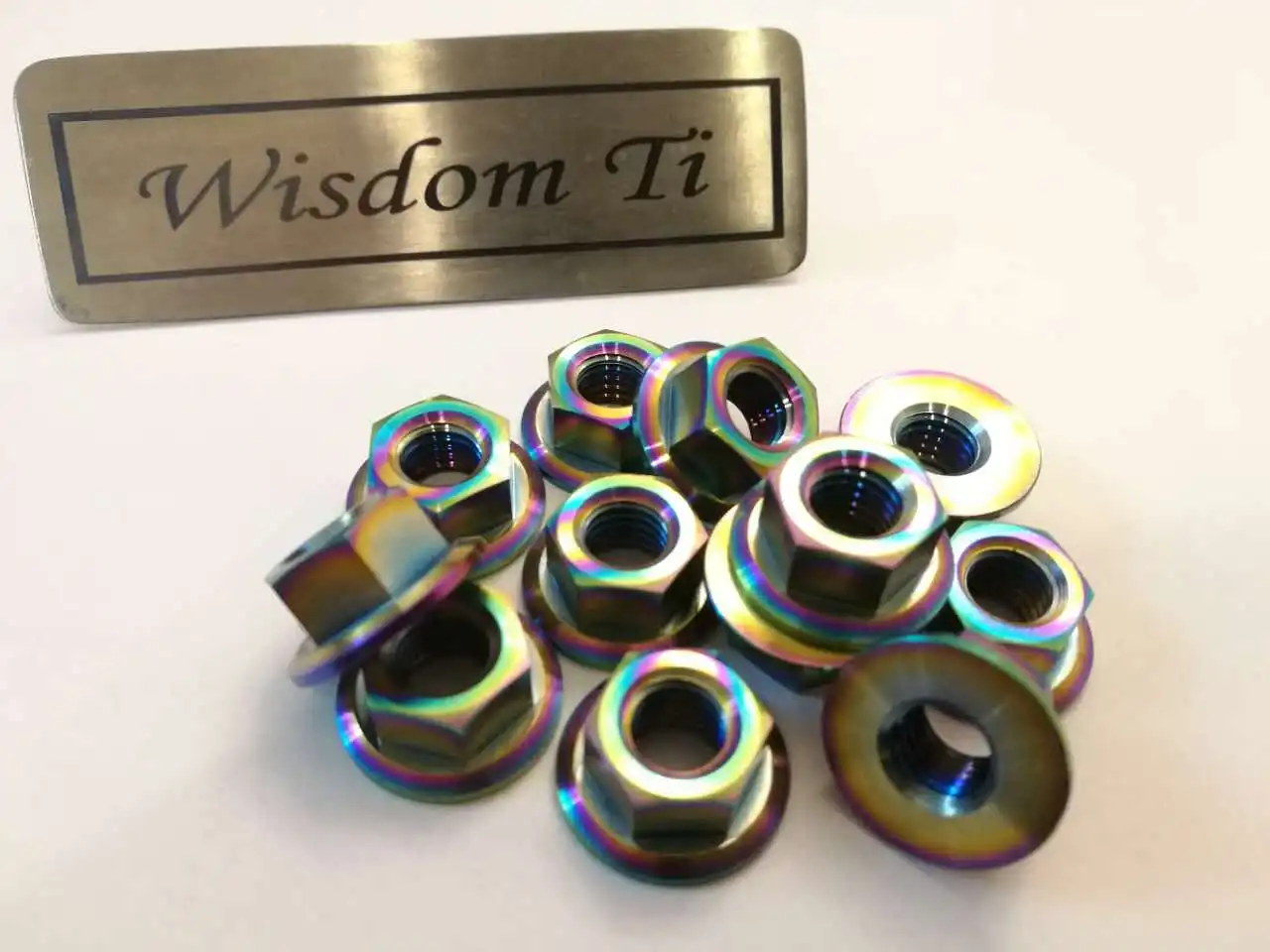
As an expert in the assembling business, I've frequently contemplated the similarity of titanium hex flange nut with added substance fabricating processes. In this article, I dive into the logical premise behind this inquiry, investigating the complexities of titanium's properties, the basics of added substance assembling, and whether these two components can flawlessly coordinate. Go along with me on this excursion as we uncover reality behind the similarity of titanium hex flange nut with added substance producing.
Titanium, eminent for its uncommon solidarity to-weight proportion, erosion opposition, and biocompatibility, remains as a material of decision across different enterprises, from aviation to clinical inserts. Its mechanical properties make it an ideal possibility for applications requesting superior execution under outrageous circumstances. In any case, with regards to added substance fabricating, especially procedures like specific laser dissolving (SLM) or electron shaft liquefying (EBM), questions emerge in regards to the similarity of titanium hex flange nut with these cycles.
Effect of Titanium Composite Attributes on Added substance Assembling
Due to factors like titanium alloys' high melting point and gas sensitivity, the attributes of titanium composites have a significant impact on additive manufacturing. With a softening point around 1668°C (3034°F), exact control is fundamental during the dissolving and cementing processes in added substance producing. Because titanium is susceptible to oxygen and nitrogen absorption, strict control of the manufacturing environment is necessary to preserve the material's integrity. This cautious administration is pivotal for keeping up with the quality and properties of titanium parts delivered through added substance producing methods. Legitimate treatment of these qualities assumes a key part in accomplishing ideal execution and dependability in the end results, featuring the significance of understanding and controlling the one of a kind credits of titanium combinations in the added substance producing process.
Materialness of Added substance Assembling Innovations to Titanium Compounds
The genuine nature of added substance fabricating advances to titanium composites is significant and extraordinary. By enabling the fabrication of parts layer by layer, 3D printing, in particular, has revolutionized conventional manufacturing methods. This approach takes into consideration advanced plan adaptability, decreased material waste, and fast prototyping abilities, which are all particularly invaluable while working with titanium compounds. The similarity of titanium compounds with added substance fabricating is affected by a few basic variables. These include the powder's quality, the temperature and pressure of the process, and the post-processing methods used. The unique properties and characteristics of titanium alloys are effectively leveraged in the additive manufacturing process by each of these elements, which ultimately contributes to the production of components of high quality and dependability.
Key to Conquering Difficulties: Process Enhancement and Control Procedures
The way to defeating difficulties in added substance assembling of titanium hex flange nut lies in executing hearty cycle improvement and control techniques. Specifically, tending to remaining tension and microstructural flaws in particular laser dissolving (SLM) and electron bar softening (EBM) cycles is fundamental for guaranteeing the mechanical uprightness of the material. Rapid heating and cooling cycles may result in residual stress and defects, which may compromise the final components' mechanical properties.
To work on mechanical execution and alleviate these issues, producers can make vital changes in accordance with the printing system. This includes adjusting the power of the laser, speeding up scanning, regulating the temperature of the powder bed, and fine-tuning other important parameters. Via cautiously dealing with these factors, makers can limit material wastage, diminish the event of imperfections, and at last upgrade the general quality and execution of titanium amalgam parts. This approach not just adds to more prominent productivity and cost-viability yet in addition guarantees that the fabricated parts meet rigid mechanical prerequisites, making them reasonable for a great many requesting applications.
Significance of Post-Handling Methods
Post-processing techniques like Hot Isostatic Pressing (HIP) and stress alleviation toughening play a crucial role in additive manufacturing of titanium alloys. These methods hold huge significance in guaranteeing the ideal presentation and strength of titanium hex flange nut parts by tending to key difficulties and improving basic material properties.
By effectively eliminating porosity, increasing material density, and enhancing the microstructure, Hot Isostatic Pressing (HIP) stands out as a potent method for enhancing the reliability of titanium alloy components. Through the utilization of high tension and temperature in a controlled climate, HIP not just works on the mechanical strength and respectability of the parts yet additionally adds to their general exhibition and life span.
Stress alleviation toughening simultaneously reduces residual stresses that may have accumulated during the manufacturing process, thereby improving the fatigue resistance of titanium alloy parts. The components have enhanced structural stability and improved resistance to cyclic loading as a result of strategically applying stress-relieving techniques like controlled heat treatment, which ultimately extends their operational lifespan in demanding environments.
The joined use of HIP and stress easing hardening not just refines the material qualities of titanium compound parts yet additionally guarantees a more elevated level of value, consistency, and execution. The production of robust and dependable titanium components for a wide range of industrial applications is made possible by these post-handling procedures, which are essential for reducing the risk of premature failure, improving fatigue resistance, and mitigating inherent material challenges.
Future Standpoint of Added substance Assembling Innovation
The trajectory of titanium additive manufacturing technology is poised to revolutionize the industrial landscape with its ongoing advancements and novel applications in the future. The continuous improvement of titanium hex flange nut added substance fabricating innovation isn't just extending creation abilities yet additionally reshaping the manner in which businesses approach producing processes.
The steady improvement of production capabilities made possible by advancements in titanium additive manufacturing is one important aspect of the outlook for the future. As the innovation advances, makers are acquiring the capacity to create complex calculations, multifaceted plans, and tweaked parts that take care of different industry needs. Businesses are now able to develop highly specialized and effective solutions that were previously unimaginable thanks to this expansion in production capabilities, which is opening up new opportunities for design freedom and product optimization.
In addition, titanium additive manufacturing's significant advantages of high accuracy and reproducibility are set to reshape the standards for part production. With the capacity to accomplish outstanding accuracy and consistency, producers can now create titanium composite parts with unrivaled quality and dependability. In addition to guaranteeing superior performance, this level of accuracy streamlines production procedures, resulting in increased efficiency and cost-effectiveness across a variety of industries.
Besides, the pattern towards tweaked arrangements in titanium added substance fabricating is driving industry development and advancement. This technology-focused businesses are increasingly providing custom solutions to industries like aerospace, defense, and automotive. These modified arrangements influence the adaptability and flexibility of added substance assembling to address explicit industry prerequisites, bringing about upgraded items that satisfy the remarkable needs of every area.
In conclusion, the advancements in production capabilities, precision, and custom solutions that will reshape the industrial landscape offer tremendous promise for the future of titanium additive manufacturing technology. As this innovation keeps on developing, businesses can anticipate expanded proficiency, improved item quality, and more prominent development, making ready for another period of assembling greatness and intensity.
Conclusion
In conclusion, despite the difficulties in ensuring that titanium hex flange nut and additive manufacturing are compatible, the synergies between these two technologies hold tremendous promise for manufacturing's future. With progressing innovative work endeavors, we can anticipate further upgrades in process productivity, material quality, and part execution, making ready for far and wide reception of added substance fabricating in creating titanium equipment.
If you have any desire to study titanium hex rib nuts or investigate added substance fabricating arrangements, go ahead and reach us at sales@wisdomtitanium.com. Our team of experts is committed to finding creative ways to meet your specific requirements.
References
-
Gibson, I., Rosen, D., & Stucker, B. (2010). Additive manufacturing technologies: Rapid prototyping to direct digital manufacturing. Springer Science & Business Media.
-
Rafi, H. K., Karthik, N. V., Gong, H., & Starr, T. L. (2013). Microstructures and mechanical properties of Ti-6Al-4V parts fabricated by selective laser melting and electron beam melting. Journal of Materials Engineering and Performance, 22(12), 3872-3883.
-
Gong, H., Rafi, K., Gu, H., & Starr, T. (2014). Influence of defects on mechanical properties of Ti–6Al–4V components produced by selective laser melting and electron beam melting. Materials & Design, 63, 856-863.
-
Wang, P., & Shamsaei, N. (2015). Defect evaluation in Ti-6Al-4V parts fabricated using powder bed fusion additive manufacturing processes. Journal of Materials Processing Technology, 215, 123-131.