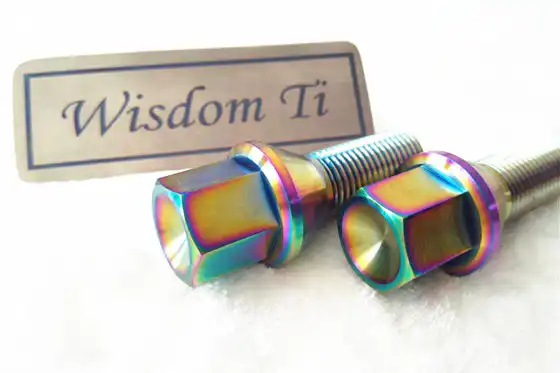
In the world of high-performance engineering, where every component plays a crucial role in ensuring safety, reliability, and optimal performance, titanium conical seat lug bolts have emerged as a game-changing solution. These specialized fasteners are designed to withstand extreme conditions and provide superior strength-to-weight ratios, making them ideal for applications in aerospace, motorsports, and other high-stress environments. In this article, we'll explore the unique properties of conical seat lug bolts and why they're becoming the go-to choice for engineers and designers in demanding industries.
Properties of Titanium Conical Seat Lug Bolts
Titanium conical seat lug bolts are engineered to provide exceptional performance in high-stress applications. Their unique combination of material properties and design features sets them apart from conventional fasteners. The use of titanium alloy in their construction offers several advantages:
- High strength-to-weight ratio: Titanium is renowned for its excellent strength while being significantly lighter than steel, making it ideal for weight-sensitive applications.
- Corrosion resistance: Titanium naturally forms a protective oxide layer, providing superior resistance to corrosion and chemical attack.
- Temperature resistance: Titanium maintains its strength and structural integrity across a wide range of temperatures, from cryogenic to elevated levels.
- Fatigue resistance: Titanium exhibits excellent fatigue properties, ensuring long-term reliability under cyclic loading conditions.
The conical seat design further enhances these inherent material benefits, creating a fastener that excels in high-stress environments. This unique geometry provides several additional advantages, which we'll explore in the next section.
How does the conical seat design enhance load distribution?
The conical seat design of these titanium lug bolts is a critical feature that sets them apart from traditional flat-seated bolts. This innovative geometry plays a significant role in improving load distribution and overall fastener performance. Here's how the conical seat design enhances load distribution:
- Increased contact area: The conical seat creates a larger surface area for contact between the bolt head and the mating surface. This expanded contact zone helps to distribute the clamping force more evenly, reducing stress concentrations that can lead to fatigue failure.
- Self-centering effect: As the bolt is tightened, the conical seat naturally guides it into the correct position. This self-centering action ensures proper alignment and consistent load distribution, even under dynamic loading conditions.
- Improved preload retention: The conical seat design helps maintain a more consistent preload over time. This is particularly important in applications subject to vibration or thermal cycling, where conventional bolts may loosen or lose clamping force.
- Reduced fretting: The conical seat minimizes relative movement between the bolt head and the mating surface, reducing the likelihood of fretting wear and corrosion.
These benefits combine to create a fastener that not only distributes loads more effectively but also maintains its performance characteristics over extended periods, even in the most demanding environments. The enhanced load distribution provided by the conical seat design is particularly beneficial in applications where uneven loading or high vibration levels are present, such as in aerospace and motorsports.
Why are Titanium Conical Seat Lug Bolts ideal for motorsports and aerospace?
The unique properties of titanium conical seat lug bolts make them exceptionally well-suited for the demanding requirements of motorsports and aerospace applications. These industries prioritize performance, safety, and weight reduction, all of which are addressed by the use of these specialized fasteners.
In motorsports:
- Weight reduction: Every gram counts in racing, and the use of titanium lug bolts can contribute to significant weight savings, particularly when multiplied across numerous fasteners in a vehicle.
- Improved performance: The reduced weight and superior strength of titanium bolts can lead to better handling, acceleration, and overall vehicle performance.
- Durability: The fatigue resistance and corrosion resistance of titanium ensure that these bolts can withstand the repeated stress cycles and harsh conditions encountered in racing environments.
- Quick changes: The self-centering nature of the conical seat design facilitates faster and more reliable wheel changes during pit stops, a critical factor in many racing disciplines.
In aerospace:
- Weight savings: In aircraft design, every kilogram saved translates to improved fuel efficiency and increased payload capacity. Titanium lug bolts offer significant weight reduction compared to steel alternatives.
- Thermal stability: Aerospace applications often involve extreme temperature variations. Titanium's ability to maintain its properties across a wide temperature range makes it ideal for these conditions.
- Corrosion resistance: Aircraft are exposed to various corrosive environments, from high-altitude atmospheric conditions to de-icing chemicals. Titanium's natural corrosion resistance helps ensure long-term reliability.
- Fatigue performance: The cyclic loading experienced by aircraft structures demands fasteners with excellent fatigue resistance. Titanium conical seat lug bolts excel in this regard, providing long-term structural integrity.
The combination of material properties and design features makes titanium conical seat lug bolts an optimal choice for both motorsports and aerospace applications. Their ability to provide superior performance while reducing weight and ensuring long-term reliability aligns perfectly with the demanding requirements of these high-tech industries.
How do these bolts reduce wear and tear in high-load applications?
Titanium conical seat lug bolts are engineered to minimize wear and tear in high-load applications through a combination of material properties and design features. This reduction in wear and tear is crucial for maintaining the integrity of critical components and extending the service life of assemblies in demanding environments. Here's how these bolts achieve this:
- Superior material hardness: Titanium alloys used in these bolts typically have a higher hardness than many conventional bolt materials. This increased hardness helps resist surface wear and deformation under high loads.
- Galling resistance: Titanium has inherent galling resistance, which reduces the likelihood of adhesive wear between the bolt and mating surfaces. This is particularly important in applications where frequent assembly and disassembly are required.
- Optimal stress distribution: The conical seat design ensures a more even distribution of stresses, reducing localized wear points that can occur with flat-seated bolts. This even distribution helps maintain the integrity of both the bolt and the mating surface over time.
- Reduced fretting wear: The increased contact area and improved load distribution of the conical seat design minimize micro-movements between surfaces. This reduction in relative motion significantly decreases fretting wear, a common issue in high-vibration environments.
- Corrosion resistance: By resisting corrosion, titanium bolts maintain their dimensional stability and surface finish over time. This preserves the tight tolerances and surface quality necessary for optimal load bearing and reduces the risk of accelerated wear due to corrosion-induced surface irregularities.
- Fatigue resistance: The superior fatigue properties of titanium, combined with the stress-distributing effects of the conical seat, result in bolts that can withstand a higher number of load cycles before showing signs of fatigue-related wear.
These factors work together to create a fastening solution that not only performs exceptionally well under high loads but also maintains its integrity over extended periods. By reducing wear and tear, titanium conical seat lug bolts help minimize maintenance requirements, extend component life, and enhance overall system reliability in critical applications.
Contact Wisdom Titanium
Titanium conical seat lug bolts represent a significant advancement in fastener technology for high-stress environments. Their unique combination of material properties and innovative design makes them an ideal choice for applications where performance, reliability, and weight reduction are paramount. From the racetrack to the skies, these specialized fasteners are proving their worth by enhancing load distribution, reducing wear and tear, and contributing to overall system efficiency.
As industries continue to push the boundaries of performance and durability, the adoption of advanced materials and designs like conical seat lug bolts will play an increasingly crucial role. Engineers and designers working on high-performance projects should consider these fasteners as a valuable tool in their arsenal for creating safer, more efficient, and more reliable systems.
If you're looking to elevate your next project with the superior performance of conical seat lug bolts, don't hesitate to reach out to the experts at Wisdom Titanium. Our team is ready to assist you in selecting the right fasteners for your specific application and ensuring you get the most out of this cutting-edge technology. Contact us today at sales@wisdomtitanium.com to discuss how we can help optimize your high-stress applications with our premium titanium fastening solutions.
References
- Campbell, F.C. (2006). Manufacturing Technology for Aerospace Structural Materials. Elsevier Science.
- Bickford, J.H. (2007). Introduction to the Design and Behavior of Bolted Joints, Fourth Edition. CRC Press.
- Peters, M., Kumpfert, J., Ward, C.H., & Leyens, C. (2003). Titanium alloys for aerospace applications. Advanced Engineering Materials, 5(6), 419-427.
- Budynas, R.G., & Nisbett, J.K. (2020). Shigley's Mechanical Engineering Design, 11th Edition. McGraw-Hill Education.