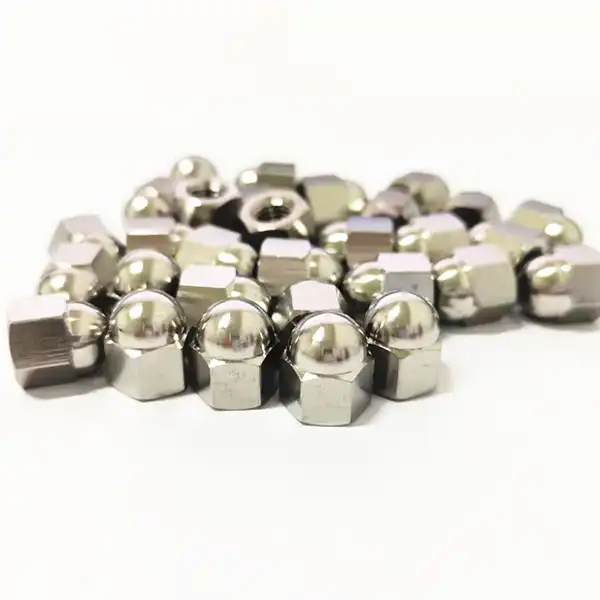
As an automotive engineer, my pursuit revolves around identifying materials that deliver both longevity and high performance. Within the domain of fastening solutions, titanium cap nuts have surfaced as an intriguing option. Their distinctive characteristics position them as an optimal contender for diverse automotive applications, offering advantages that outstrip conventional materials such as steel or aluminum. This article aims to delve into the scientific underpinnings driving the favoritism towards titanium cap nuts in automotive engineering, accentuating their primary benefits and practical deployment across real-world scenarios. By exploring the unique attributes of titanium cap nuts and their implications for automotive systems, this discussion endeavors to illuminate the rationale underpinning their prominence in the industry and their potential to elevate the performance and durability of automotive components.
Understanding Titanium Cap Nuts
Titanium, celebrated for its remarkable strength-to-weight ratio, resistance to corrosion, and compatibility with biological systems, has gained extensive traction across aerospace, medical, and automotive sectors. Among the array of fastening solutions, cap nuts stand out as pivotal components characterized by a domed cap that conceals the visible end of a bolt or screw. Within automotive assemblies, cap nuts assume a critical function in upholding structural stability and dependability. Their integration not only enhances the aesthetic appeal of assemblies but also reinforces their robustness. By leveraging the unparalleled properties of titanium in conjunction with the strategic use of cap nuts, automotive engineers can optimize the performance and longevity of vehicle components. This synergy underscores the significance of selecting premium materials and fastening solutions to uphold the integrity and reliability of automotive systems in diverse operational environments.
Strength and Durability
The decision to opt for titanium cap nuts primarily stems from their outstanding strength attribute. Titanium, despite weighing around 45% less than steel, showcases equivalent or enhanced tensile strength levels. This unique strength-to-weight ratio offers a significant advantage by reducing overall mass while preserving structural robustness, a critical factor in improving fuel efficiency and enhancing the general performance of vehicles.
Furthermore, titanium's natural resistance to corrosion guarantees durability even in challenging operational conditions, like exposure to road salts, moisture, and varying temperatures. In contrast to their steel counterparts, titanium cap nuts fend off rust and deterioration, ensuring prolonged integrity throughout extensive periods of utilization. The corrosion-resistant properties of titanium not only contribute to longevity but also alleviate maintenance requirements, making it an ideal choice for applications demanding reliability and longevity in adverse environmental settings.
Heat Resistance
In automotive contexts, fasteners frequently encounter heightened temperatures arising from engine operations or exhaust systems. Titanium's exceptional heat resistance and high melting point render it highly suitable for such rigorous conditions. In contrast to conventional materials that may weaken or distort when exposed to thermal stress, titanium cap nuts maintain their mechanical characteristics, guaranteeing dependable performance even in extreme temperature environments. This resilience to heat-induced degradation underscores titanium's value as a material of choice for automotive applications, particularly in areas where exposure to elevated temperatures is a prevalent concern. By leveraging the heat-resistant properties of titanium cap nuts, automotive engineers can enhance the reliability and longevity of fastening solutions, contributing to the overall durability and performance of vehicle components in challenging thermal environments.
Reduced Maintenance and Lifecycle Costs
The exceptional durability of titanium cap nuts leads to decreased maintenance needs and reduced lifecycle expenses for both automotive manufacturers and end-users. Due to extended service intervals and minimal susceptibility to corrosion-related issues, vehicles outfitted with titanium fasteners encounter fewer instances of downtime and incur lower maintenance costs, ultimately leading to overall cost savings over the vehicle's lifetime. This longevity and reliability not only benefit manufacturers by reducing warranty claims and enhancing customer satisfaction but also offer end-users the advantage of lower ownership costs and enhanced operational dependability. By minimizing the need for frequent maintenance and addressing potential failure points, the integration of titanium cap nuts in automotive applications contributes to a more efficient, cost-effective, and reliable vehicle ownership experience.
Enhanced Performance
In high-performance automotive scenarios, the weight and performance attributes of each component play pivotal roles in shaping overall vehicle dynamics. Through the adoption of titanium cap nuts, engineers can realize weight reductions without sacrificing structural integrity, thereby bolstering acceleration, handling, and braking capabilities. Additionally, the diminished unsprung weight serves to enhance suspension responsiveness, ultimately delivering a more immersive and engaging driving experience. The strategic integration of titanium cap nuts not only contributes to improved vehicle agility and performance but also underscores the potential for heightened driver satisfaction and confidence behind the wheel. This emphasis on weight optimization and performance enhancement reflects a commitment to elevating the driving experience in high-performance automotive contexts, aligning with the pursuit of precision, efficiency, and dynamic prowess in vehicle design and engineering.
Real-World Applications
The utilization of titanium cap nuts in automotive engineering spans a wide array of applications, encompassing engine parts, chassis, and suspension setups. Particularly in high-performance vehicles, titanium fasteners play a pivotal role in critical areas like exhaust manifolds, intake systems, and suspension components, prioritizing weight reduction and longevity.
Moreover, titanium cap nuts see significant use in electric vehicles (EVs), where lightweight design is crucial for maximizing operational range and energy efficiency. Through the reduction of overall vehicle mass, titanium fasteners aid in prolonging battery life and optimizing power consumption, thereby bolstering the practicality and attractiveness of electric propulsion technologies. This integration of titanium components underscores their versatile benefits across different automotive segments, aligning with industry trends towards enhanced performance, sustainability, and energy efficiency in modern vehicle design and development.
Conclusion
In summary, the choice of titanium cap nuts in automotive engineering is driven by their exceptional blend of strength, longevity, heat tolerance, and weight-saving attributes. Through harnessing the distinctive properties of titanium, engineers can enhance vehicle performance, durability, and lifespan while reducing maintenance needs and overall expenses. Whether in high-performance sports cars or environmentally-conscious electric vehicles, titanium cap nuts serve as key components influencing the trajectory of automotive design and advancement. Their versatile benefits cater to a wide range of automotive applications, contributing to improved efficiency, reliability, and sustainability across the industry. As automotive technology continues to evolve, the utilization of titanium cap nuts underscores a commitment to innovation, performance optimization, and the pursuit of excellence in modern vehicle engineering practices.
If you want to learn more about titanium cap nuts, welcome to contact us: sales@wisdomtitanium.com.
References
- Boyer, R. R. (1996). An overview on the use of titanium in the aerospace industry. Materials Science and Engineering: A, 213(1-2), 103-114.
- Lütjering, G., & Williams, J. C. (2007). Titanium (2nd ed.). Springer Science & Business Media.
- Niinomi, M. (2008). Recent metallic materials for biomedical applications. Metallurgical and Materials Transactions A, 39(6), 1348-1354.
- Wang, J., & Moroz, A. (2012). Overview of advanced materials and lightweight structures for marine vehicles. Ocean Engineering, 48, 504-518.