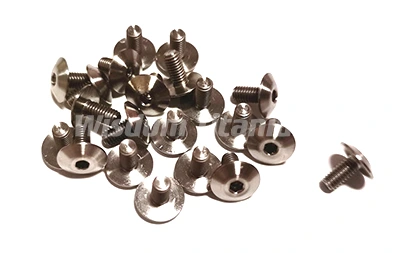
After collaborating for an extended period as a professional engineer in the industry of aerospace, I have come to recognize the critical role of individual components in ensuring the successful completion of every endeavor in this line of work. Considering the numerous components that refer to a fighter jet or spacecraft, screws could not initially appear like an essential component. Whatever the outcome, deciding on the kind of component for these unpretentious connectors can have an important influence on the general performance of the car, continuous servicing, and comfort of the mental state. In the following article, I am going to discuss the reasons—supported by both industry understanding and scientific data—why m3 titanium screws have grown into the standard option in the aerospace industry.
Understanding Titanium
It must be understood to first comprehend the characteristics that render titanium exceptional before analyzing the exact explanations behind its being utilized in aeronautical fasteners. The chemically formed element titanium is well-known for possessing a remarkable strength-to-weight ratio, durability against oxidation, and biologic compatibility. These properties contribute to it being an ideal choice for an assortment of programs, from high-performance aviation elements to implants for medicine.
Titanium has a superb strength-to-weight percentage, which is one of the primary factors contributing to its popularity in the aerospace industry. Compared to steel, titanium is significantly lighter while still maintaining impressive strength. This feature is essential for aircraft design, as it is necessary for preserving lightness without compromising the integrity of the framework.
In addition, titanium has been employed in airplane nails primarily as a result of its durability against weathering. The extreme climatic variables that aircraft undergo exposure to, such as overbearing temperature and moisture variations, may speed up erosion. Titanium's ability to resist corrosion ensures the longevity and reliability of aerospace components, making it a preferred material for critical applications.
Furthermore, titanium's biocompatibility is advantageous in medical implant applications. When used in implants such as joint replacements or dental implants, titanium minimizes the risk of adverse reactions within the body. Its ability to integrate well with biological tissues makes it a safe and effective choice for medical devices.
In the realm of high-performance aircraft components, titanium's unique properties shine. Its high strength allows for the construction of lightweight yet durable parts that can withstand the demands of flight. Whether in engine components, structural elements, or fasteners like screws, titanium plays a vital role in enhancing aircraft performance and safety.
In conclusion, titanium's exceptional strength-to-weight ratio, corrosion resistance, and biocompatibility make it a versatile material with a wide range of applications. From aerospace screws to medical implants, titanium's unique properties contribute to its widespread use in various industries, highlighting its importance in modern engineering and technology.
Strength and Lightweight
One of the most compelling reasons for using m3 titanium screws in aerospace engineering is their remarkable strength-to-weight ratio. Unlike traditional materials like steel or aluminum, titanium offers comparable strength while being significantly lighter. This characteristic is crucial in aerospace applications, where every gram of weight matters. By utilizing titanium screws, engineers can achieve substantial weight savings without compromising structural integrity or performance.
Corrosion Resistance
Cold temperatures, considerable amounts of moisture, and coming into contact with acidic substances are characteristics of the hostile surroundings in which aerospace engines perform. In such conditions, materials susceptible to corrosion pose a significant risk to the integrity of the aircraft or spacecraft. Titanium's exceptional corrosion resistance makes it an attractive choice for fasteners, ensuring long-term reliability and durability in demanding operating environments. Whether it's battling saltwater exposure in marine aircraft or withstanding the corrosive effects of rocket propellants, m3 titanium screws offer unparalleled protection against degradation.
Temperature Resistance
The materials' aptitude for withstanding extremes of temperature is a further vital asset in aeronautical operations. From the freezing cold of outer space to the blistering heat generated during supersonic flight, aerospace components must perform reliably across a wide range of thermal conditions. Titanium exhibits exceptional temperature resistance, remaining stable and structurally sound even in environments with extreme heat or cold. This attribute is particularly advantageous in applications where traditional materials would deform or fail under thermal stress, ensuring the continued functionality of critical fasteners.
Fatigue Resistance
In the demanding operating conditions of aerospace vehicles, components are subjected to cyclic loading and fatigue stress that can lead to material fatigue and eventual failure. Titanium's superior fatigue resistance makes it an ideal choice for screws and fasteners, providing an added layer of reliability and safety. Whether it's enduring repeated cycles of pressurization and depressurization in an aircraft cabin or withstanding the vibrational forces experienced during launch and re-entry, m3 titanium screws exhibit remarkable endurance against fatigue failure.
Biocompatibility
The potential for biocompatibility of titanium is worth pointing out, particularly within the setting of life support systems and space exploration by humans, even though it is not immediately relevant to all aeronautical usages. When astronauts come into contact with gold-containing materials or medical implants, for example, their physical makeup will be suitable for titanium owing to its biocompatibility, which reduces the potential for adverse responses or medical problems.
Conclusion
In the end, titanium screws are the building block preferred for aircraft construction owing to their unequaled bravery, light weight, resistance to corrosion, temperature compassion, wear and tear acceptance, and biologic compatibility. On account of their outstanding attributes, titanium screws are a crucial component of aerospace and aeronautical buildings, where reliability, effectiveness, and security are all important aspects. Titanium is expected to have a far greater role when choosing the direction of aerospace design as long as technology continues to evolve and ambitious missions to outer space persist.
If you want to learn more about m3 titanium screws, welcome to contact us: sales@wisdomtitanium.com.
References
-
Boyer, R. R. (1996). An overview on the use of titanium in the aerospace industry. Materials Science and Engineering: A, 213(1-2), 103-114.
-
Lütjering, G., & Williams, J. C. (2007). Titanium. Springer Science & Business Media.
- Sanders, T. H., & Simmons, J. A. (1999). Fasteners, materials, and corrosion-resistant alloys for aerospace applications. In Handbook of Materials Selection (pp. 237-275). John Wiley & Sons.
- Williams, J. C. (2003). Titanium. Springer Science & Business Media.