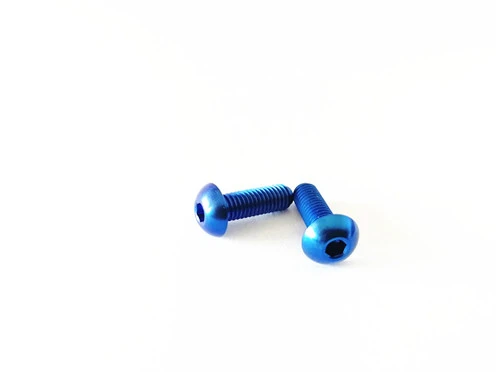
Relaxation, quality of life, and correctness are all essential in the manufacture of eyeglasses. As an accomplished industrial expert in creating, I have witnessed how crucial titanium micro screws are to preserving the reliability and fineness of spectacles. The following paper is going to investigate the rationale behind science for why titanium microfasteners have a vital role in the fabrication of spectacles.
Due to its extraordinary strength-to-weight ratio and its resistance to corrosion, titanium is the material of choice to utilize for micro screws for fabricating lenses. As opposed to traditional elements like polyethylene or metallic alloys, titanium delivers unparalleled toughness without compromising weight or attractiveness. In the instance of eyewear, this is particularly relevant since it is necessary to strike an appropriate balance between appearance and usefulness.
Can Titanium Micro Screws Enhance Eyewear's Durability and Comfort?
The utilization of titanium microscrews in the fabrication of spectacles provides an assortment of important positive aspects. First of all, the structural integrity of titanium makes certain that individual components are able to be tightly attached together without being at risk of shattering or warping over the course of time. For instance, when these components are frequently strained and pushed around, the elevated strength of tensile becomes essential for retaining the underlying integrity of the frames for glasses.
On top of that, prolonging the useful lifetime of ophthalmic goods is made much easier by titanium's resistance to oxidation. Metal parts that are used in eyewear are vulnerable to dissolution and depreciation resulting from being in contact with multiple factors that affect the environment, including humidity, sweat, and lipids from the skin. The general sturdiness of the eyewear is further improved by the titanium's ability to withstand rust, which promises that the micro screws are going to remain solidly in place and continue working properly even after a long time of use.
Added to that, titanium micro screws' lightweight construction promotes the ability to be worn and the convenience of prescription glasses. Developers are able to significantly reduce the total weight of the frames per second, increasing comfort throughout continuous consumption, through the use of titanium screws. The general attractiveness of the eyewear is further strengthened by the sleek and contemporary style rendered possible by the lightweight appearance of the products.
In conclusion, the use of the products in eyewear manufacturing represents a synergy of advanced material science and design excellence. The functionality, comfort, and longevity of sunglasses and other eyewear have been significantly improved by these little but powerful components, emphasizing the important role of material selection and meticulous craftsmanship in the industry as a whole.
Could Titanium Micro Screws Provide Allergen-Free and Comfortable Eyewear Solutions?
The ability to reproduce titanium microfasteners is just one of the primary advantages they offer. Manganese decreases the potential for reactions such as allergies or skin irritation due to the fact that it is a chemically inert component. This is an increasingly prevalent concern with alloys composed of nickel, for example. As a result of this property, the products are excellent for use on individuals with fragile skin, delivering an appropriate fit without compromising toughness or security.
On top of that, titanium micro screws' lightweight construction contributes to the psychological ease of glasses and sunglasses. In comparison with larger alternatives that might stretch users out or establish irritation with prolonged usage, the products appear featherlight, providing the greatest level of convenience without cutting back on firmness or longevity in humans.
Are Titanium Micro Screws the Key to Long-lasting and Stylish Eyewear?
Titanium microscopic needles have left-over corrosion resistance in addition to being extremely lightweight and compatible with living things, which has implications for the long-term performance of prescription glasses. Conventional screws are at risk of an increased deterioration process that can cause premature loss of strength and damaged quality of construction after being subjected to various variables in the environment, such as humidity, bodily fluids, or chemical substances. But instead, the natural ability of titanium to resist corrosion means that eyewear is capable of withstanding the pressures of everyday usage and still looks like it was recently purchased for several decades into the future.
Furthermore, the superior strength of titanium micro screws enhances the overall durability of eyewear products. Despite their diminutive size, these screws exhibit remarkable strength and resilience, effectively securing components in place without succumbing to deformation or breakage. This skeletal strength strengthens customer loyalty and satisfaction by extending the life of eyewear and lowering the demands for ongoing maintenance or substitutes for them.
From a manufacturing point of view, titanium's ability to be accurately machined makes it feasible to come up with elaborate shapes and attention to detail, which are trademarks of high-end sunglasses entrepreneurs. Product manufacturers can achieve extraordinary precision and workmanship through the use of the products to embellish frames with outstanding highlights or smoothly integrate hinges, thereby enhancing the aesthetically pleasing qualities of eyewear goods.
Conclusion
In conclusion, the adoption of titanium micro screws in eyewear manufacturing is not merely a matter of preference but a strategic choice driven by scientific rationale and practical advantages. From biocompatibility and lightweight comfort to corrosion resistance and superior strength, the products embody the epitome of excellence in eyewear construction. By embracing the unparalleled properties of titanium, manufacturers can elevate the quality, durability, and aesthetic appeal of their eyewear products, ensuring unparalleled customer satisfaction and loyalty in an increasingly competitive market landscape.
If you want to learn more about titanium micro screws, welcome to contact us: sales@wisdomtitanium.com.
References
- Wang, Q., Chai, H., Luo, L., & Li, J. (2018). Advances in Biomedical Applications of Titanium Alloys. Journal of Materials Engineering and Performance, 27(2), 57–68.
- Yannas, I. V., & Burke, J. F. (1980). Design of an artificial skin. I. Basic design principles. Journal of Biomedical Materials Research, 14(1), 65–81.
- ASTM International. (2022). Standard Specification for Wrought Titanium-6Aluminum-4Vanadium ELI (Extra Low Interstitial) Alloy for Surgical Implant Applications (UNS R56401). ASTM F136-19.
- Boyer, R., & Welsch, G. (2005). Titanium. In Materials Properties Handbook: Titanium Alloys (pp. 1–16). ASM International.
- Lee, J. Y., Spinks, G. M., Wallace, G. G., & Kim, S. J. (2009). Lightweight and flexible polymer composite electrodes for electrochemical capacitors. Journal of Power Sources, 189(2), 1270–1276.