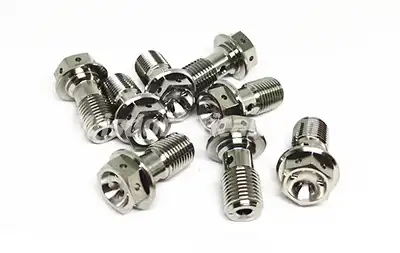
The titanium banjo bolt is one of the best examples of engineering excellence in high-performance automotive components. Because of their exceptional strength and resistance to corrosion, these specialty fasteners are essential to fuel and brake systems. However, what is so unique about these bolts? Let's examine the cutting-edge technologies used to produce these meticulously designed parts.
Fully CNC Machined With Rolled Threads
titanium banjo bolts are made using an advanced manufacturing technique that blends accuracy and productivity. Computer Numerical Control (CNC) machining, a technology that has completely changed the manufacturing sector, is at the center of this process.
CNC machining is perfect for producing titanium banjo bolts because it can create intricate shapes with remarkable precision. A solid titanium bar is used as the starting point for the procedure, and it is meticulously shaped using incredibly accurate computer-controlled cutting tools. Because these multi-axis machines can remove material with micron-level accuracy, every bolt's surface, diameter, and contour will meet the necessary specifications. In addition to shaping the bolt's head and body, the cutting tools are programmed to create the intricate internal passages that are essential to its operation. This degree ofaccuracy guarantees that every titanium banjo bolt operates at its best, fitting precisely and providing dependable strength, improving the overall functionality and longevity of
The titanium banjo bolt's threads are among its most important features. These bolts have rolled threads, in contrast to conventional cutting techniques. In order to create the thread profile, the metal is compressed using a cold-forming technique called thread rolling. This method has a number of benefits:
Strengthening: By work-hardening the metal through rolling, a stronger thread is produced.
Better surface finish: The smoother surface of rolled threads lessens wear and friction.
Increased fatigue resistance: Under cyclic loading, rolled threads' constant grain flow increases durability.
A titanium banjo bolt that satisfies exacting dimensional specifications and provides exceptional mechanical qualities is the product of CNC machining and thread rolling. This degree of accuracy is necessary to guarantee appropriate sealing and functionality in critical fluids.
Material Selection and Heat Treatment
titanium banjo bolt material selection is not random. Usually, Grade 5 titanium alloy, or Ti-6Al-4V, is used to make these parts. Because of its remarkable strength-to-weight ratio, resistance to corrosion, and biocompatibility, this alloy is highly valued.
The titanium alloy Ti-6Al-4V has trace amounts of other elements in addition to its main constituents of 4% vanadium and 6% aluminum. These extra components, which include trace amounts of iron, oxygen, and nitrogen, enhance the alloy's overall strength, resistance to corrosion, and ability to withstand heat. Ti-6Al-4V has a tensile strength of 900–1050 MPa (130,000–152,000 psi), making it ideal for high-stress applications requiring outstanding performance and durability. For vital parts like car braking systems, where the alloy's capacity to tolerate high forces, fend off wear, and preserve structural integrity in the face of adversity is essential for dependability and safety, this makes it the perfect material.
Heat treatment procedures are frequently used to further improve the titanium alloy's qualities. These therapies may consist of:
- Solution treating is the process of creating a supersaturated solid solution by heating the alloy to a certain temperature and then quickly cooling it.
Aging: The material is strengthened by controlled heating that permits precipitates to form.
To get the ideal ratio of toughness, ductility, and strength, the heat treatment procedure is meticulously regulated. This guarantees that the titanium banjo bolt's structural integrity won't be compromised even under the extreme pressures and temperatures found in automotive systems.
Surface Treatment
Although titanium banjo boltsare naturally resistant to corrosion, titanium banjo bolts can benefit from additional surface treatments to improve both their functionality and appearance. These therapies accomplish several goals:
1. Anodizing: This electrochemical procedure covers the titanium's surface with a thin, protective oxide layer. In addition to increasing the bolt's resistance to corrosion, anodizing can be used to give it color, which makes it simpler to distinguish between different sizes or grades. Additionally, the anodized layer offers some electrical insulation, which is advantageous in some situations.
2. Passivation: This chemical procedure improves titanium's inherent resistance to corrosion by removing free iron from its surface. In harsh environments, passivation is especially crucial for preserving the bolt's integrity.
3. Dry film lubricants: The titanium banjo bolt's threads may occasionally be coated with a thin coating of solid lubricant. Galling is a type of wear brought on by adhesion between sliding surfaces under heavy loads, and this lessens friction during installation.
4. Shot peening: This mechanical procedure applies a layer of compressive stress to the bolt's surface by bombarding it with tiny spherical media. The titanium banjo bolt's fatigue life can be greatly increased by shot peening, which increases its resistance to stress corrosion cracking and cyclic loading.
Specialized surface treatments greatly improve the titanium banjo bolt's overall performance and longevity by offering more defense against environmental stress, corrosion, and wear. These processes, which include anodizing or coating with ceramic or diamond-like carbon (DLC), produce a strong outer layer that increases the bolt's resistance to oxidation and abrasion. This guarantees that the bolt will retain its structural integrity and continue to function dependably even in the face of harsh circumstances, such as high temperatures, exposure to moisture, or high pressure settings. These treatments contribute to the titanium banjo bolt's longer service life by improving its surface hardness and resistance to chemical deterioration, which lessens the need for frequent replacements and increases the system's overall durability.
Conclusion
To sum up, the titanium banjo bolt is a combination of cutting-edge materials science and manufacturing techniques. Every step of its manufacturing process, from the accuracy of CNC machining and thread rolling to the cautious selection and handling of titanium alloys, is focused on producing a component that excels in strength, durability, and dependability. The technologies underlying these vital parts will surely develop as automotive systems continue to change, pushing the limits of mechanical engineering's capabilities.
Selecting a manufacturer with a track record of excellence is essential for anyone looking to purchase premium titanium banjo bolts. With a minimum order quantity of 200 pieces, Wisdom Titanium, an ISO 9001-certified manufacturer, specializes in creating premium titanium banjo bolts. Their proficiency in material science and CNC machining guarantees that every bolt satisfies the highest requirements for performance and quality. Interested parties can reach Wisdom Titanium at sales@wisdomtitanium.com to place an order or for additional information.
References
Groover, M. P. (2010). Fundamentals of Modern Manufacturing: Materials, Processes, and Systems. John Wiley & Sons.
Leyens, C., & Peters, M. (Eds.). (2003). Titanium and Titanium Alloys: Fundamentals and Applications. John Wiley & Sons.
ASM International. (2000). ASM Handbook, Volume 5: Surface Engineering. ASM International.