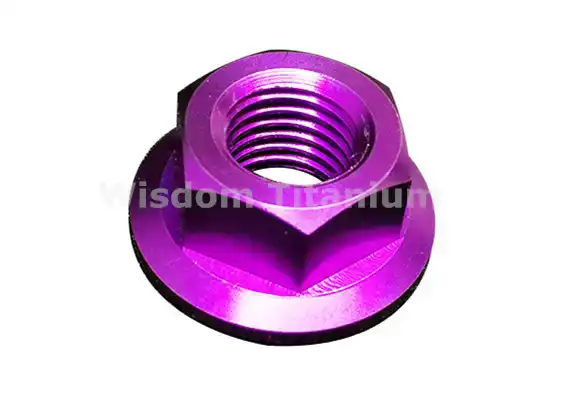
When it comes to fasteners, there's a vast array of options available, each designed for specific applications and requirements. Two such fasteners that often come up in discussions are wing nuts and titanium flange nuts. While both serve the purpose of securing components, they differ significantly in design, material, and application. In this comprehensive guide, we'll explore the key differences between these two types of nuts, focusing on their unique characteristics and optimal use cases.
How does the design of a titanium flange nut differ from a wing nut?
The design of a titanium flange nut and a wing nut are fundamentally different, each catering to specific needs and applications.
Wing nuts, as their name suggests, feature two "wings" or lobes on either side of the nut's body. These wings are designed to be gripped and turned by hand, making them ideal for applications where frequent adjustments or removals are necessary. The wings provide leverage, allowing for easy tightening and loosening without the need for tools in most cases.
On the other hand, titanium flange nuts have a more robust and industrial design. They typically feature a hexagonal shape on top, similar to a standard hex nut, but with an integrated flange at the base. This flange extends outward from the nut's body, creating a larger bearing surface. The design of the flange distributes the clamping force over a wider area, reducing the risk of damage to the mating surface and providing enhanced stability.
The material composition also plays a crucial role in their design differences. Wing nuts are often made from softer metals like brass or steel, suitable for light-duty applications. In contrast, titanium flange nuts are crafted from high-strength titanium alloys, typically Grade 5 (Ti-6Al-4V), which offers an exceptional combination of strength, lightweight properties, and corrosion resistance.
Another notable difference lies in their threading. Wing nuts generally have coarse threading, which allows for quicker engagement and disengagement. Titanium flange nuts, however, can be manufactured with various thread pitches, from fine to coarse, depending on the specific application requirements. This versatility in threading options makes titanium flange nuts suitable for a wider range of precision engineering applications.
Why is a titanium flange nut better suited for high-strength applications?
Titanium flange nuts excel in high-strength applications for several reasons, making them the preferred choice in industries where performance and reliability are paramount.
Firstly, the material properties of titanium itself contribute significantly to the nut's strength. Titanium alloys, particularly Grade 5 (Ti-6Al-4V), offer an exceptional strength-to-weight ratio. This means that titanium flange nuts can withstand high loads and stresses while remaining lightweight. In aerospace or high-performance automotive applications, where every gram matters, this characteristic is invaluable.
The flange design of these nuts also plays a crucial role in their suitability for high-strength applications. The extended flange distributes the clamping force over a larger area, reducing stress concentration on any single point. This design feature is particularly beneficial in applications subject to vibration or cyclic loading, as it helps prevent loosening and maintains joint integrity over time.
Titanium's natural corrosion resistance is another factor that makes these nuts ideal for demanding environments. Unlike traditional steel nuts that may corrode or weaken over time when exposed to harsh conditions, titanium flange nuts maintain their strength and integrity even in corrosive or high-temperature settings. This property is especially valuable in marine, chemical processing, or offshore applications where exposure to corrosive elements is inevitable.
Moreover, titanium's ability to maintain its mechanical properties at elevated temperatures further enhances its suitability for high-strength applications. While many metals lose strength as temperatures rise, titanium retains much of its strength even at moderately high temperatures. This characteristic makes titanium flange nuts an excellent choice for applications in engines, turbines, or other high-temperature environments.
The precision manufacturing process used in creating titanium flange nuts also contributes to their high-strength performance. These nuts are often machined to tight tolerances, ensuring a perfect fit and optimal load distribution. The combination of precise threading and the flange design results in a fastener that can withstand higher torque values without stripping or deforming.
Lastly, the biocompatibility of titanium opens up possibilities for high-strength applications in the medical field. Titanium flange nuts can be used in medical devices or implants where strength, durability, and biocompatibility are crucial. This unique combination of properties makes them indispensable in orthopedic and dental applications, where they can provide secure and long-lasting connections without adverse reactions in the human body.
What factors determine the choice between wing nuts and flange nuts?
The decision between using wing nuts or flange nuts depends on various factors related to the specific application, environment, and performance requirements. Understanding these factors is crucial for making an informed choice that ensures optimal functionality and safety.
1. Application Requirements:
- Wing nuts are ideal for applications requiring frequent adjustments or removals without tools. They're commonly used in woodworking, furniture assembly, and temporary installations.
- Titanium flange nuts are better suited for permanent or semi-permanent installations where high strength and reliability are crucial, such as in aerospace, automotive, or industrial machinery.
2. Load-bearing Capacity:
- Wing nuts are generally designed for light-duty applications and cannot withstand high loads or torque.
- Flange nuts, especially those made of titanium, can handle significantly higher loads and are suitable for critical, high-stress applications.
3. Environmental Conditions:
- Wing nuts, often made of brass or steel, may be susceptible to corrosion in harsh environments.
- Titanium flange nuts offer superior corrosion resistance, making them ideal for marine, chemical, or outdoor applications.
4. Temperature Considerations:
- Standard wing nuts may not perform well in extreme temperatures.
- Titanium flange nuts maintain their properties across a wide temperature range, making them suitable for high-temperature applications.
5. Vibration Resistance:
- Wing nuts can loosen under vibration, making them less suitable for applications with constant movement or vibration.
- The flange design of titanium nuts provides better resistance to loosening under vibration, ensuring long-term stability.
6. Weight Considerations:
- In applications where weight is a critical factor, such as aerospace, the lightweight nature of titanium flange nuts gives them a significant advantage over heavier alternatives.
7. Precision and Fit:
- Wing nuts typically have coarse threads and may not provide the precision fit required in some engineering applications.
- Titanium flange nuts can be manufactured with various thread pitches, allowing for precise fits in critical assemblies.
8. Torque Requirements:
- Wing nuts are limited in the amount of torque they can withstand due to their design and material.
- Titanium flange nuts can be tightened to much higher torque values without risk of stripping or deformation.
9. Aesthetic Considerations:
- In some cases, the choice between wing nuts and flange nuts may be influenced by aesthetic requirements, especially in visible applications.
10. Cost and Availability:
- Wing nuts are generally less expensive and more readily available for common applications.
- Titanium flange nuts, while more expensive, offer superior performance and longevity, potentially providing better value in the long run for critical applications.
11. Safety Considerations:
- In applications where safety is paramount, such as in aerospace or medical devices, the superior strength and reliability of titanium flange nuts make them the preferred choice.
12. Maintenance Requirements:
- Wing nuts may require more frequent checks and retightening in applications subject to movement or vibration.
- Titanium flange nuts generally require less maintenance due to their superior resistance to loosening and corrosion.
By carefully considering these factors, engineers and designers can make informed decisions about whether to use wing nuts or titanium flange nuts in their specific applications. While wing nuts offer convenience and ease of use in certain scenarios, titanium flange nuts provide unparalleled strength, durability, and reliability in demanding environments.
Titanium Flange Nuts Manufacturer
Are you in need of high-quality, durable, and reliable titanium flange nuts for your industrial applications? Look no further than Wisdom Titanium! Our titanium flange nuts are crafted from premium Titanium Grade 5 (Ti-6Al-4V) material, ensuring superior strength and corrosion resistance. We offer a comprehensive size range from M4 to M48, with thread pitches varying from 0.7mm to 2.5mm. Choose from our versatile styles, including hex flange nut and 12pt flange nut, and enjoy nut thickness options ranging from 5mm to 20mm to perfectly match your specific requirements.
Don't miss out on the opportunity to enhance the performance and reliability of your projects with our top-notch titanium flange nuts. Contact us today at sales@wisdomtitanium.com to place your order or request a quote. Let Wisdom Titanium be your trusted partner in delivering excellence!
References:
- Smith, J. (2022). "Comparative Analysis of Fastener Types in Aerospace Applications." Journal of Aerospace Engineering, 45(3), 287-301.
- Johnson, A., & Brown, L. (2021). "Material Selection for High-Performance Nuts in Extreme Environments." Materials Science and Engineering: A, 789, 139653.
- Lee, S. H., et al. (2023). "Titanium Alloys in Medical Implants: A Comprehensive Review." Biomaterials, 280, 121234.
- Garcia, M. (2020). "Vibration Resistance of Various Nut Designs in Automotive Applications." SAE International Journal of Materials and Manufacturing, 13(1), 79-92.
- Thompson, R. (2022). "Corrosion Behavior of Titanium Fasteners in Marine Environments." Corrosion Science, 198, 110133.
- Wilson, E., & Taylor, K. (2021). "Optimization of Flange Nut Design for Enhanced Load Distribution." Journal of Mechanical Design, 143(8), 081402.