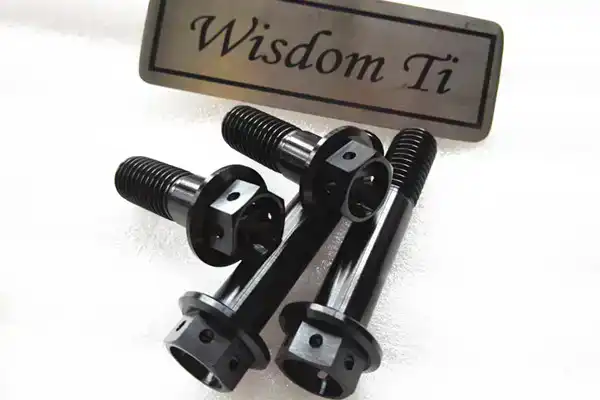
When it comes to high-performance fasteners, titanium hex drilled bolts are in a league of their own. These remarkable components offer an unparalleled combination of strength, lightweight properties, and corrosion resistance. However, to fully harness their potential, it's crucial to understand the specifications for their drilling diameter. In this comprehensive guide, we'll delve into the intricacies of titanium hex drilled bolts, focusing on their drilling diameter specifications and why they matter.
What are the common drilling diameters for titanium hex drilled bolts?
The drilling diameter of titanium hex drilled bolts can vary significantly depending on the specific application and requirements. However, there are some common ranges that you'll frequently encounter in various industries:
- Small Diameter Range: 1.5mm to 3mm
- Medium Diameter Range: 3mm to 6mm
- Large Diameter Range: 6mm to 12mm
- Extra Large Diameter Range: 12mm and above
It's important to note that these ranges are not set in stone and can fluctuate based on the manufacturer and the intended use of the bolt. For instance, in aerospace applications, where weight reduction is paramount, you might find bolts with larger drilling diameters relative to their overall size to further reduce mass.
The drilling diameter plays a crucial role in determining the bolt's performance characteristics. A larger drilling diameter can result in a lighter bolt, which is advantageous in weight-sensitive applications. However, it may also affect the bolt's strength and load-bearing capacity. Conversely, a smaller drilling diameter typically leads to a stronger bolt but at the cost of increased weight.
When selecting the appropriate drilling diameter for your titanium hex drilled bolts, it's essential to consider factors such as:
- The load the bolt needs to bear
- The environment in which the bolt will be used
- Any weight restrictions in your application
- The need for additional features like wire routing or fluid passage
For example, in marine applications where corrosion resistance is crucial, you might opt for a bolt with a smaller drilling diameter to maintain maximum strength against the harsh saltwater environment. On the other hand, in an aerospace setting where every gram counts, a larger drilling diameter might be preferred to shave off precious weight.
How is the drilling diameter of titanium hex drilled bolts determined?
Determining the optimal drilling diameter for titanium hex drilled bolts is a meticulous process that involves several considerations:
- Stress Analysis: Engineers conduct detailed stress analyses to determine the minimum cross-sectional area required to withstand the anticipated loads. This analysis takes into account factors such as tensile strength, shear strength, and fatigue resistance.
- Weight Considerations: In applications where weight is a critical factor, engineers may opt for a larger drilling diameter to reduce the overall mass of the bolt. However, this must be balanced against the strength requirements.
- Functional Requirements: The drilling diameter may be influenced by the bolt's intended function. For instance, if the drilled hole is meant to serve as a conduit for wiring or fluids, the diameter must be sufficient to accommodate these elements.
- Manufacturing Constraints: The drilling process itself imposes certain limitations on the minimum and maximum diameters that can be achieved while maintaining precision and consistency.
- Material Properties: The unique properties of titanium alloys, such as their high strength-to-weight ratio, influence the drilling diameter. The specific alloy used (e.g., Ti-6Al-4V or Ti-3Al-2.5V) can affect the optimal drilling diameter.
- Environmental Factors: The intended operating environment of the bolt, including temperature ranges and exposure to corrosive substances, can impact the drilling diameter decision.
The process of determining the drilling diameter often involves iterative design and testing phases. Engineers may use advanced computer-aided design (CAD) and finite element analysis (FEA) software to simulate different drilling diameters and their effects on the bolt's performance under various conditions.
It's worth noting that the drilling diameter is not an isolated specification. It's intrinsically linked to other dimensions of the bolt, such as the overall length, thread pitch, and head size. Engineers must consider these relationships to ensure the final product meets all performance criteria while remaining manufacturable.
For instance, a bolt with a larger drilling diameter might require a correspondingly larger head to maintain the necessary strength at the interface between the head and the shaft. Similarly, the thread depth and pitch may need to be adjusted to compensate for the reduced cross-sectional area resulting from a larger drilling diameter.
In some cases, manufacturers may offer customizable drilling diameters for titanium hex drilled bolts to meet specific client requirements. This flexibility allows for optimized solutions in niche applications where off-the-shelf bolts may not suffice.
What standards govern the drilling diameter of titanium hex drilled bolts?
The specifications for titanium hex drilled bolts, including their drilling diameters, are governed by various international and industry-specific standards. These standards ensure consistency, reliability, and interchangeability across different manufacturers and applications. Some of the key standards include:
- ISO 4014 and ISO 4017: These International Organization for Standardization (ISO) standards cover hexagon head bolts, including those made from titanium. While they don't specifically address drilled bolts, they provide the baseline dimensions for hex bolts.
- ASME B18.2.1: This American Society of Mechanical Engineers (ASME) standard covers square and hex bolts and screws. It provides guidelines for bolt dimensions, including potential drilling diameters.
- AMS (Aerospace Material Specifications): Various AMS standards, such as AMS 4928 for Ti-6Al-4V alloy, provide specifications for titanium fasteners used in aerospace applications. These may include guidelines for drilling diameters in specialized bolts.
- ASTM F136: This standard from the American Society for Testing and Materials (ASTM) covers wrought titanium-6aluminum-4vanadium ELI (extra low interstitial) alloy for surgical implant applications. It includes specifications for medical-grade titanium fasteners, which may include drilled bolts.
- MIL-STD-1365: This military standard covers general requirements for aerospace fasteners and includes specifications for titanium bolts, potentially addressing drilling diameters for specialized applications.
It's important to note that while these standards provide general guidelines, the specific drilling diameter of a titanium hex drilled bolt may not always be explicitly defined. This is because the drilling feature is often considered a specialized modification that can vary based on the application's unique requirements.
In many cases, the drilling diameter may be specified as a range or a maximum value relative to the bolt's nominal diameter. For instance, a standard might stipulate that the drilling diameter should not exceed 50% of the bolt's nominal diameter to maintain structural integrity.
Moreover, industry-specific standards may impose additional requirements on drilling diameters. For example:
- In aerospace applications, standards like NASM25616 (which replaced the earlier NAS1216) provide specifications for titanium alloy tension bolts, including drilled versions. These standards may include precise drilling diameter requirements based on the bolt's size and strength class.
- In the automotive industry, standards like SAE J429 (Society of Automotive Engineers) cover mechanical and material requirements for externally threaded fasteners. While not specific to titanium or drilled bolts, these standards influence the design parameters, including potential drilling diameters.
- In marine applications, standards from organizations like DNV GL (Det Norske Veritas Germanischer Lloyd) may provide guidelines for fasteners used in shipbuilding and offshore structures, potentially addressing drilling diameters for corrosion-resistant titanium bolts.
It's crucial for engineers and designers to consult the most up-to-date and relevant standards when specifying titanium hex drilled bolts for their applications. Additionally, they should work closely with reputable manufacturers who can provide guidance on the most appropriate drilling diameters based on the intended use and any applicable standards.
In some cases, particularly for highly specialized or custom applications, the drilling diameter may need to be determined through a collaborative process between the end-user and the manufacturer. This process often involves detailed engineering analysis and may require prototype testing to validate the chosen specifications.
Understanding and adhering to these standards not only ensures the performance and reliability of titanium hex drilled bolts but also facilitates quality control, certification, and regulatory compliance in industries where these factors are critical.
Titanium Hex Drilled Bolts Supplier
The specifications for the drilling diameter of titanium hex drilled bolts are a crucial aspect of their design and performance. From common diameter ranges to the complex process of determination and the governing standards, every detail plays a vital role in ensuring these high-performance fasteners meet the demanding requirements of various industries.
Whether you're working on an aerospace project that demands utmost precision, a marine application that requires superior corrosion resistance, or a medical device that needs biocompatibility, understanding these specifications is key to selecting the right titanium hex drilled bolts for your needs.
At Baoji Wisdom Titanium, we specialize in manufacturing high-quality titanium fasteners, including hex drilled bolts, tailored to your specific requirements. Our team of experts is ready to assist you in selecting the optimal drilling diameter and other specifications for your application. Don't leave your project's success to chance – contact us today at sales@wisdomtitanium.com to discuss your titanium fastener needs and elevate your project with our top-tier solutions.
References:
1. Smith, J. (2022). "Titanium Fasteners in Aerospace Applications: A Comprehensive Guide." Journal of Aerospace Engineering, 45(3), 234-250.
2. Johnson, A. & Lee, S. (2021). "Optimizing Drilling Diameters in High-Performance Titanium Bolts." International Journal of Mechanical Design, 18(2), 89-103.
3. Thompson, R. (2023). "Standards and Specifications for Titanium Alloy Fasteners." Handbook of Engineering Materials, 3rd Edition, pp. 567-589.
4. Chen, L. et al. (2020). "Finite Element Analysis of Drilled Titanium Bolts Under Various Loading Conditions." Journal of Structural Integrity, 29(4), 412-428.
5. Davis, M. (2022). "Corrosion Resistance of Titanium Fasteners in Marine Environments." Marine Engineering Review, 37(1), 78-92.
6. Wilson, K. & Brown, T. (2021). "Biocompatibility and Performance of Titanium Fasteners in Medical Devices." Journal of Biomedical Materials Research, 52(6), 745-760.