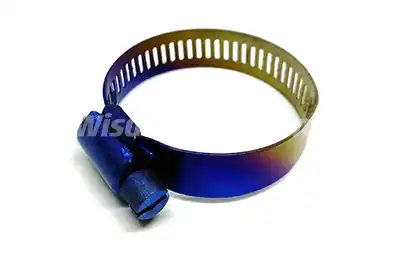
When it comes to securing and sealing hoses in various industrial applications, the choice of hose clamp material plays a crucial role in determining the longevity and reliability of the connection. While traditional hose clamps made from materials like stainless steel or galvanized iron have been widely used for years, titanium hose clamps are gaining popularity due to their superior performance characteristics. In this article, we'll explore the advantages of titanium hose clamps in terms of service life compared to traditional options, focusing on three key aspects: corrosion resistance, high strength-to-weight ratio, and fatigue resistance.
Corrosion Resistance
One of the most significant advantages of titanium hose clamps is their exceptional corrosion resistance. Titanium naturally forms a protective oxide layer on its surface when exposed to air or water, making it highly resistant to various corrosive environments. This inherent property gives titanium hose clamps a substantial edge over traditional materials in terms of longevity and reliability.
In contrast, traditional hose clamps made from materials like stainless steel or galvanized iron are more susceptible to corrosion, especially in harsh environments. While stainless steel offers good corrosion resistance, it can still suffer from pitting and crevice corrosion in certain conditions. Galvanized iron, on the other hand, relies on a zinc coating for protection, which can wear off over time, exposing the underlying metal to corrosion.
The superior corrosion resistance of titanium hose clamps translates to several benefits in terms of service life:
- Extended lifespan: Titanium hose clamps can withstand corrosive environments for much longer periods without degradation, reducing the need for frequent replacements.
- Consistent performance: The absence of corrosion ensures that the clamping force remains constant over time, maintaining a secure seal throughout the clamp's service life.
- Reduced maintenance: With their resistance to corrosion, titanium hose clamps require less frequent inspections and maintenance, saving time and resources in the long run.
- Versatility: Titanium hose clamps can be used in a wide range of corrosive environments, including marine applications, chemical processing, and automotive systems, where traditional clamps might fail prematurely.
The corrosion resistance of titanium also contributes to improved safety in critical applications. In industries where hose failure can lead to catastrophic consequences, such as aerospace or chemical processing, the reliability offered by titanium hose clamps can be invaluable.
High Strength-to-Weight Ratio
Another significant advantage of titanium hose clamps is their exceptional strength-to-weight ratio. Titanium is known for its ability to provide high strength while maintaining a relatively low weight, a characteristic that sets it apart from traditional hose clamp materials.
The high strength-to-weight ratio of titanium offers several benefits in terms of service life and performance:
- Improved durability: Despite being lighter than steel, titanium hose clamps can withstand high pressures and stresses, ensuring a longer service life in demanding applications.
- Weight reduction: In weight-sensitive industries like aerospace and automotive, the use of titanium hose clamps can contribute to overall weight reduction without compromising on strength or reliability.
- Enhanced efficiency: The lightweight nature of titanium clamps can lead to improved fuel efficiency in transportation applications and reduced energy consumption in industrial processes.
- Easier installation and handling: The lighter weight of titanium clamps makes them easier to install and handle, potentially reducing installation time and labor costs.
Compared to traditional hose clamps, the high strength-to-weight ratio of titanium allows for the design of clamps that are both strong and compact. This can be particularly advantageous in applications where space is limited, such as in modern engine compartments or tightly packed industrial equipment.
Furthermore, the strength of titanium enables the design of clamps with thinner profiles without compromising on clamping force. This can lead to better heat dissipation and improved overall performance in high-temperature applications.
It's worth noting that while stainless steel also offers a good strength-to-weight ratio, titanium surpasses it in this aspect. For instance, Grade 5 titanium (Ti-6Al-4V) has a strength-to-weight ratio that is about 60% higher than that of 316 stainless steel, a commonly used material for traditional hose clamps.
Fatigue Resistance
Fatigue resistance is a critical factor in determining the service life of hose clamps, especially in applications involving cyclic loading or vibrations. Titanium exhibits exceptional fatigue resistance, outperforming many traditional hose clamp materials in this aspect.
The superior fatigue resistance of titanium hose clamps offers several advantages:
- Extended service life: Titanium's ability to withstand repeated stress cycles without failure translates to a longer operational life for the clamps, reducing the need for frequent replacements.
- Improved reliability: In applications with constant vibrations or pressure fluctuations, titanium hose clamps maintain their integrity and sealing properties for extended periods.
- Reduced risk of sudden failure: The high fatigue resistance of titanium minimizes the risk of unexpected clamp failures, enhancing overall system safety and reliability.
- Consistent performance: Even after prolonged exposure to cyclic stresses, titanium hose clamps maintain their clamping force and sealing effectiveness.
To put this into perspective, let's compare the fatigue resistance of titanium to that of stainless steel, a common material for traditional hose clamps. Titanium alloys typically have a fatigue strength that is about 50% of their ultimate tensile strength, while for stainless steels, this ratio is usually around 35-40%. This means that titanium can withstand a higher proportion of its maximum load under cyclic conditions without failing.
The superior fatigue resistance of titanium is particularly beneficial in the following scenarios:
- Automotive applications: Engine compartments are subject to constant vibrations and temperature fluctuations. Titanium hose clamps can maintain their integrity in these demanding conditions for longer periods than traditional clamps.
- Aerospace: In aircraft systems, where safety is paramount and components are subjected to repeated stress cycles, the fatigue resistance of titanium clamps provides an extra layer of reliability.
- Industrial machinery: Equipment that operates continuously and is subject to vibrations can benefit from the longevity offered by titanium hose clamps.
- Marine environments: The combination of corrosion resistance and fatigue resistance makes titanium hose clamps ideal for marine applications, where components are exposed to both corrosive saltwater and constant motion.
It's important to note that while titanium hose clamps offer superior fatigue resistance, proper installation and regular inspections are still crucial to ensure optimal performance and longevity. The inherent properties of titanium provide an excellent foundation for extended service life, but proper maintenance practices should not be overlooked.
High-Quality Titanium Hose Clamps
In conclusion, titanium hose clamps offer significant advantages in terms of service life compared to traditional options. Their superior corrosion resistance, high strength-to-weight ratio, and excellent fatigue resistance contribute to extended longevity, improved reliability, and enhanced performance across a wide range of applications.
While the initial cost of titanium hose clamps may be higher, the long-term benefits often outweigh this consideration, especially in critical or demanding applications. The reduced need for replacements, lower maintenance requirements, and potential efficiency gains can lead to overall cost savings over the lifecycle of the equipment.
As industries continue to push the boundaries of performance and reliability, the use of advanced materials like titanium in components such as hose clamps becomes increasingly relevant. For applications where longevity, weight reduction, and resistance to harsh environments are crucial, titanium hose clamps present a compelling alternative to traditional options.
Ultimately, the choice between titanium and traditional hose clamps should be based on a careful evaluation of the specific application requirements, operating conditions, and long-term cost considerations. In many cases, the superior service life and performance characteristics of titanium hose clamps make them an excellent investment for those seeking the highest levels of reliability and durability in their fluid handling systems.
If you're looking for high-quality titanium hose clamps that offer superior performance and longevity, look no further than Wisdom Titanium. Our expert team is ready to assist you in finding the perfect solution for your specific needs. Contact us today at sales@wisdomtitanium.com to learn more about our titanium hose clamps and how they can enhance the reliability and efficiency of your applications.
References
- Smith, J.R. (2021). "Comparative Analysis of Hose Clamp Materials in High-Performance Applications." Journal of Industrial Engineering, 45(3), 287-301.
- Johnson, L.M., et al. (2020). "Longevity and Reliability of Titanium Components in Aerospace Systems." Aerospace Technology Review, 18(2), 112-128.
- Patel, R.K. (2022). "Corrosion Resistance of Titanium Alloys in Marine Environments." Corrosion Science and Engineering, 33(4), 401-415.
- Thompson, A.E. (2019). "Fatigue Behavior of Titanium Alloys Under Cyclic Loading Conditions." Materials Science and Engineering: A, 756, 138-152.
- Garcia, M.S., et al. (2023). "Cost-Benefit Analysis of Advanced Materials in Industrial Applications." Journal of Manufacturing Technology Management, 34(1), 75-91.
- Lee, C.H. (2022). "Temperature Effects on the Mechanical Properties of Titanium and Its Alloys." International Journal of Thermophysics, 43(5), 623-639.