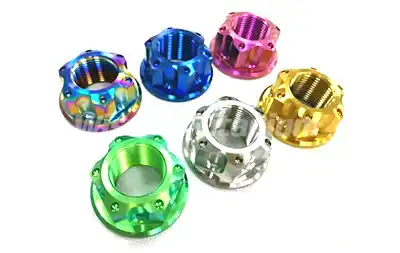
Axle nuts play a crucial role in securing wheels to vehicles, from bicycles to motorcycles and even cars. These small but mighty components are responsible for keeping your wheels firmly in place, ensuring safe and smooth rides. But have you ever wondered what materials are used to create these essential parts? In this comprehensive guide, we'll explore the various materials used for axle nuts, with a special focus on the benefits of titanium rear axle nuts.
What materials are commonly used for axle nuts?
Axle nuts are manufactured using a variety of materials, each with its own set of properties and advantages. The choice of material depends on factors such as the vehicle type, intended use, and performance requirements. Here are some of the most common materials used for axle nuts:
1. Steel
Steel is the most widely used material for axle nuts, particularly in standard vehicles. It offers excellent strength and durability at a relatively low cost. Steel axle nuts come in various grades, including carbon steel and alloy steel, each offering different levels of strength and corrosion resistance. For instance, grade 8 steel axle nuts are known for their high tensile strength and are often used in heavy-duty applications.
2. Stainless Steel
Stainless steel axle nuts are favored for their superior corrosion resistance. They're particularly useful in environments where rust and oxidation are concerns, such as in coastal areas or on boats. While not as strong as some high-grade carbon steels, stainless steel offers a good balance of strength and corrosion resistance.
3. Aluminum
Aluminum axle nuts are lightweight alternatives to steel, making them popular in racing and performance applications where weight reduction is crucial. However, they're generally not as strong as steel and may require more frequent replacement. Aluminum axle nuts are often anodized to improve their corrosion resistance and aesthetic appeal.
4. Titanium
Titanium axle nuts, including titanium rear axle nuts, are at the top end of the spectrum in terms of performance and cost. They offer an exceptional strength-to-weight ratio, corrosion resistance, and durability. While more expensive than other options, titanium axle nuts are increasingly popular in high-performance vehicles, motorcycles, and racing applications.
Why is titanium a preferred material for axle nuts?
Titanium has gained significant popularity as a material for axle nuts, particularly in high-performance and racing applications. But what makes titanium rear axle nuts so special? Let's delve into the unique properties that make titanium a preferred choice:
1. Exceptional Strength-to-Weight Ratio
Titanium boasts an impressive strength-to-weight ratio, surpassing that of steel. This means that titanium rear axle nuts can provide the same or even greater strength than steel nuts while weighing significantly less. In the world of racing and high-performance vehicles, where every gram counts, this property is invaluable.
2. Corrosion Resistance
Titanium is highly resistant to corrosion, even in harsh environments. Unlike steel, which can rust, or aluminum, which can corrode, titanium forms a protective oxide layer on its surface when exposed to oxygen. This natural protection makes titanium rear axle nuts ideal for use in various conditions, from everyday street riding to off-road adventures.
3. Durability and Longevity
The combination of strength and corrosion resistance makes titanium axle nuts exceptionally durable. They can withstand high stress, vibration, and temperature variations without degrading. This longevity can translate to lower maintenance costs and fewer replacements over time, despite the higher initial investment.
4. Temperature Resistance
Titanium maintains its strength and structural integrity even at high temperatures. This property is particularly beneficial in racing applications, where components can be subjected to extreme heat. Titanium rear axle nuts can handle these conditions without compromising their performance or safety.
5. Aesthetic Appeal
Beyond its functional benefits, titanium also offers an aesthetic advantage. Its distinctive gray color and matte finish give it a sleek, high-tech appearance that many enthusiasts appreciate. Some manufacturers even offer colored titanium axle nuts through anodizing processes, allowing for customization.
How does material choice impact axle nut durability and strength?
The choice of material for axle nuts significantly influences their durability and strength, which in turn affects the overall performance and safety of the vehicle. Let's examine how different materials compare in terms of these crucial factors:
1. Tensile Strength
Tensile strength is a measure of how much force a material can withstand before breaking. In this regard, high-grade steel and titanium are top performers. For instance, grade 5 titanium (commonly used for titanium rear axle nuts) has a tensile strength of about 900 MPa, which is comparable to or higher than many steels. This high tensile strength ensures that the axle nut can withstand the significant forces exerted during acceleration, braking, and cornering.
2. Fatigue Resistance
Axle nuts are subjected to cyclic loading, which can lead to fatigue over time. Titanium excels in this area, with superior fatigue resistance compared to steel and aluminum. This means that titanium rear axle nuts are less likely to develop cracks or fail due to repeated stress cycles, contributing to their longevity and reliability.
3. Corrosion Resistance
Corrosion can significantly impact the durability of axle nuts. While stainless steel offers good corrosion resistance, titanium is superior in this aspect. The natural oxide layer that forms on titanium provides excellent protection against various types of corrosion, including galvanic corrosion when in contact with other metals. This property ensures that titanium rear axle nuts maintain their integrity even in harsh environments.
4. Weight Considerations
The weight of axle nuts, while seemingly insignificant, can impact vehicle performance, especially in racing applications. Aluminum axle nuts are the lightest but sacrifice some strength. Titanium offers an optimal balance, being about 40% lighter than steel while maintaining comparable or superior strength. This weight reduction, when considered across all components, can contribute to improved acceleration and handling.
5. Thermal Properties
The ability to maintain strength and structural integrity at high temperatures is crucial for axle nuts, particularly in high-performance applications. Titanium outperforms both steel and aluminum in this regard, retaining its strength at higher temperatures. This property ensures that titanium rear axle nuts remain reliable even under extreme conditions, such as those encountered in racing or heavy-duty use.
6. Cost and Long-Term Value
While the initial cost of titanium axle nuts is higher than steel or aluminum alternatives, their durability and longevity can offer better long-term value. The reduced need for replacements and the potential performance benefits can offset the higher upfront investment, especially for enthusiasts and professional racers.
In conclusion, the choice of material for axle nuts is a critical decision that impacts not only the component's durability and strength but also the overall performance and safety of the vehicle. While steel remains a popular and cost-effective choice for many applications, titanium rear axle nuts offer superior performance characteristics that make them an excellent choice for those seeking the ultimate in strength, durability, and weight savings.
If you're looking to upgrade your vehicle's performance with high-quality titanium components, consider exploring the benefits of titanium rear axle nuts. For expert advice and custom titanium solutions, don't hesitate to reach out to us at sales@wisdomtitanium.com. Our team is ready to help you find the perfect titanium components to elevate your vehicle's performance and durability.
References
- SAE International. (2019). SAE J429: Mechanical and Material Requirements for Externally Threaded Fasteners.
- ASM International. (2008). ASM Handbook, Volume 1: Properties and Selection: Irons, Steels, and High-Performance Alloys.
- Kaufman, J. G. (2000). Introduction to Aluminum Alloys and Tempers. ASM International.
- Lutjering, G., & Williams, J. C. (2007). Titanium (2nd ed.). Springer-Verlag Berlin Heidelberg.
- Donachie, M. J. (2000). Titanium: A Technical Guide (2nd ed.). ASM International.