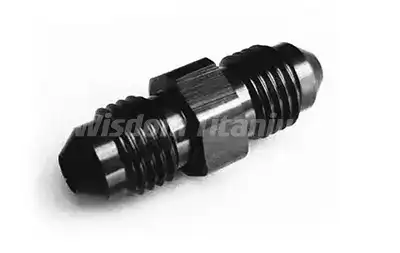
When it comes to manufacturing high-quality titanium banjo adapters, the method used to create threads plays a crucial role in determining the overall performance and durability of the component. Two common techniques for thread formation are cutting and rolling. In this article, we'll explore the advantages of rolled threads compared to cut threads in titanium banjo adapters, focusing on increased strength, better fatigue resistance, and improved thread profile.
Increased Strength
One of the primary advantages of rolled threads in titanium banjo adapters is their superior strength compared to cut threads. The rolling process involves cold-forming the metal, which results in a significant increase in the thread's tensile strength. This enhancement is particularly beneficial for banjo adapters, which are often subjected to high pressures and stresses in various applications.
During the rolling process, the metal's grain structure is compressed and aligned along the thread's contours. This realignment of the grain structure leads to a more uniform distribution of stress throughout the thread, reducing the likelihood of weak points that could lead to failure. As a result, titanium banjo adapters with rolled threads can withstand higher loads and pressures, making them ideal for demanding applications in industries such as aerospace, automotive, and high-performance motorsports.
Moreover, the increased strength of rolled threads allows for the use of smaller thread sizes without compromising the overall integrity of the titanium banjo adapter. This can lead to weight savings and more compact designs, which are often crucial factors in engineering and product development. The ability to maintain strength while reducing size and weight makes rolled threads an attractive option for manufacturers looking to optimize their titanium banjo adapter designs.
Better Fatigue Resistance
One of the most notable advantages of employing rolled threads in titanium banjo adapters is their exceptional fatigue resistance. Fatigue failure is a phenomenon that occurs when materials are subjected to repeated cyclic loading, even when the applied stresses are below the material’s yield strength. This type of failure is particularly problematic in applications where components are regularly exposed to vibrations, temperature fluctuations, and varying pressures—conditions that titanium banjo adapters frequently encounter in demanding environments.
The rolling process used to create threads results in a significantly smoother surface finish compared to traditional cutting methods. This improvement in surface quality is critical because it reduces surface roughness and, consequently, minimizes stress concentration points. These points are often the starting locations for fatigue cracks, which can lead to premature failure. By reducing these imperfections, rolled threads inherently contribute to the longevity of the components.
Moreover, the cold-working effect that occurs during the thread rolling process introduces beneficial compressive residual stresses in the outer layers of the titanium material. These compressive stresses act as a formidable barrier against crack propagation, further enhancing the fatigue resistance of the titanium banjo adapter. The combined effect of a smoother surface and the introduction of residual stresses results in a component that can withstand cyclic loading for a significantly longer period.
The improved fatigue resistance associated with rolled threads directly translates into an extended service life for titanium banjo adapters. This increased durability not only leads to lower maintenance requirements and reduced replacement costs but also enhances the overall reliability of systems utilizing these adapters. In critical applications, such as aerospace or medical devices, the enhanced fatigue resistance provided by rolled threads offers an invaluable layer of safety and peace of mind, ensuring that these essential components perform reliably over time.
Improved Thread Profile: Enhancing Performance and Reliability
The thread profile is a critical factor in determining the performance and reliability of a titanium banjo adapter. Rolled threads offer several advantages in this regard, contributing to improved functionality and easier assembly.
One of the key benefits of rolled threads is their superior surface finish. The rolling process produces a smoother thread surface compared to cutting, which reduces friction during assembly and disassembly. This smoother surface also improves the sealing properties of the titanium banjo adapter, which is crucial in applications where leak prevention is paramount.
Furthermore, rolled threads typically exhibit better dimensional consistency and accuracy compared to cut threads. The rolling process allows for tighter control over thread dimensions, resulting in more precise fits and improved interchangeability between components. This precision is particularly valuable in industries where standardization and quality control are critical, such as in the production of medical devices or aerospace components.
Another advantage of the improved thread profile in rolled threads is the potential for increased thread engagement. The cold-forming process used in thread rolling can create a slightly larger minor diameter compared to cut threads, resulting in a greater surface area for load distribution. This increased engagement can lead to improved load-bearing capacity and enhanced resistance to stripping or thread failure in titanium banjo adapters.
Conclusion
In conclusion, rolled threads offer several significant advantages over cut threads in titanium banjo adapters. The increased strength, better fatigue resistance, and improved thread profile contribute to enhanced performance, reliability, and longevity of these critical components. As manufacturers and engineers continue to push the boundaries of design and performance, the benefits of rolled threads make them an attractive choice for high-quality titanium banjo adapters.
At Wisdom Titanium, we understand the importance of these advantages in manufacturing superior titanium banjo adapters. As an ISO 9001-certified manufacturer and supplier of standard and customized CNC parts since 2013, we pride ourselves on using high-grade titanium and advanced manufacturing techniques to deliver exceptional products. If you're in the market for top-quality titanium banjo adapters or other precision components, we invite you to experience the Wisdom Titanium difference. Contact us at sales@wisdomtitanium.com to learn more about how our expertise in rolled thread technology can benefit your projects.
References
1.Bhattacharya, A., & Das, S. (2019). A review on the machinability improvement of titanium alloy. Reviews on Advanced Materials Science, 58(1), 1-20.
2.Neves, R. S., Silva, F. J. G., Ferreira, L. P., Pereira, T., Gouveia, R. M., & Pimentel, C. (2020). Improving the quality and productivity of rolled threads for the automotive industry. Procedia Manufacturing, 51, 442-449.
3.Domblesky, J. P., & Feng, F. (2002). A parametric study of process parameters in external thread rolling. Journal of Materials Processing Technology, 121(2-3), 341-349.