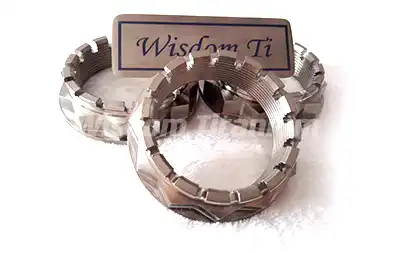
The titanium rear wheel nut M48 is a critical component in high-performance vehicles and racing applications, where strength, lightweight properties, and reliability are paramount. This comprehensive guide explores the intricate manufacturing process of these specialized fasteners, from initial design considerations to final quality control measures. Understanding this process is essential for engineers, manufacturers, and automotive enthusiasts who rely on these components for optimal vehicle performance and safety.
Design And Planning
The production of titanium rear wheel nuts begins with a meticulous design and planning phase. Engineers utilize advanced Computer-Aided Design (CAD) software to create detailed technical drawings that specify exact dimensions, threading specifications, and load-bearing requirements. The M48 designation indicates a metric thread with a 48mm nominal diameter, requiring precise calculations to ensure proper engagement and torque specifications.
During this phase, engineers consider various factors including operating conditions, stress analysis, and safety margins. The design must account for the specific vehicle application, including factors such as wheel size, hub configuration, and anticipated loads. Material selection focuses primarily on Grade 5 titanium alloy (Ti-6Al-4V), chosen for its exceptional strength-to-weight ratio and excellent mechanical properties.
The planning stage also involves determining manufacturing processes, tooling requirements, and production schedules. Engineers must consider the unique challenges of working with titanium, including its high strength, low thermal conductivity, and tendency to work hard during machining.
Material Preparation And Processing
The material preparation process begins with the extraction of titanium from rutile and ilmenite ores through the Kroll process. Raw titanium undergoes multiple refinement stages to create a titanium sponge, which is then melted and alloyed with 6% aluminum and 4% vanadium to produce Ti-6Al-4V ingots. These ingots are subsequently converted into bars or billets through various forging operations.
The machining process typically involves multiple steps on CNC (Computer Numerical Control) equipment. Initial operations include turning operations to establish the basic hexagonal shape and length. Advanced multi-axis machining centers are employed to create precise threading, which is critical for proper torque application and load distribution. The threading process often utilizes specialized cutting tools and cooling strategies to manage the heat generated during machining.
Special attention is paid to chip control and cutting parameters due to titanium's unique properties. Machining speeds are typically slower than those used for steel, with higher feed rates and abundant cooling to prevent work hardening and ensure optimal surface finish.
Heat Treatment And Surface Treatment
Heat treatment and surface treatment are critical steps in the manufacturing of titanium rear wheel nut M48, as they enhance mechanical properties, durability, and resistance to environmental factors. These processes are meticulously designed to ensure that the titanium wheel nuts meet demanding performance and longevity requirements in high-stress applications.
Heat Treatment Process
Heat treatment plays a pivotal role in tailoring the mechanical properties of titanium, such as strength, ductility, and fatigue resistance. The process typically consists of multiple stages:
1. Solution Treatment
The heat treatment process begins with solution treatment, where the titanium wheel nuts are heated to approximately 925°C (1697°F). At this temperature, the material enters the beta phase, dissolving any precipitates and homogenizing the microstructure. Controlled cooling, either through air quenching or furnace cooling, follows this step. The controlled cooling ensures a fine and balanced alpha-beta microstructure, which is critical for achieving a combination of strength and ductility.
2. Aging Treatment
After solution treatment, aging is conducted to further optimize the mechanical properties. During this step, the material is reheated to a lower temperature, typically between 480°C and 595°C (896°F to 1103°F), and held for a specific duration. This promotes the precipitation of fine strengthening phases, such as Ti3Al or TiAl3, within the titanium matrix. The aging process enhances the ultimate tensile strength of the nuts, bringing them into the desired range of 900–1050 MPa, while preserving sufficient ductility to withstand high-stress conditions without cracking.
3. Stress Relieving (Optional)
In some cases, an additional stress-relieving step may be included to reduce residual stresses introduced during machining or forming. This minimizes the risk of distortion and enhances the fatigue resistance of the nuts.
Quality Control And Inspection
Quality control for the titanium rear wheel nut M48 is a meticulous process designed to ensure the highest levels of performance, safety, and reliability. It begins with the certification of incoming raw materials, which ensures that only premium-grade titanium alloy, meeting strict compositional requirements, is used in production. From there, rigorous inspection protocols are implemented throughout the manufacturing process to maintain compliance with industry standards and customer specifications.
Incoming Material Certification
The first step in quality control involves verifying the chemical composition and mechanical properties of the titanium alloy. This is done through material certification reports provided by suppliers and independent laboratory testing to confirm conformance to standards like ASTM B348. This step is critical as it establishes the foundation for the nut's mechanical performance and corrosion resistance.
Dimensional Inspection
Every batch of titanium rear wheel nuts undergoes thorough dimensional inspections to ensure precise manufacturing. Advanced precision measuring equipment such as coordinate measuring machines (CMM) is employed to verify critical dimensions like diameter, thread size, and overall geometry. Thread gauges are used to inspect threading specifications, including pitch, angle, and depth. These measurements guarantee compatibility with the mating components and ensure a secure fit.
Where To Buy Titanium Rear Wheel Nut M48?
For those seeking high-quality titanium rear wheel nut M48 components, Wisdom Titanium offers professional manufacturing services with comprehensive quality control and competitive pricing. Their Grade 5 titanium (Ti-6Al-4V) products feature tensile strengths ranging from 900 to 1050 MPa, meeting rigorous industry standards.
The manufacturing process employs full CNC machining with rolled threads, ensuring precise dimensional control and optimal mechanical properties. With a minimum order quantity of 100 pieces, they maintain ample stock levels to meet various production requirements. Interested parties can initiate inquiries through their sales department at sales@wisdomtitanium.com.
References
1. ASM International. (2015). Titanium: A Technical Guide, 2nd Edition.
2. Boyer, R., Welsch, G., & Collings, E.W. (2007). Materials Properties Handbook: Titanium Alloys.
3. SAE International. (2019). Aerospace Material Specification: Titanium Alloy, Sheet, Strip, and Plate.
4. Peters, M., Kumpfert, J., Ward, C.H., & Leyens, C. (2003). Titanium Alloys for Aerospace Applications.
5. ASTM International. (2021). Standard Specification for Titanium and Titanium Alloy Bars and Billets.