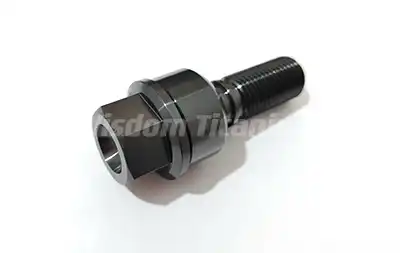
When it comes to high-performance vehicles like Porsche, every component plays a crucial role in overall performance and safety. One such component that often goes unnoticed but is vital to the vehicle's integrity is the humble lug bolt. In recent years, titanium lug bolts have gained popularity among enthusiasts and manufacturers alike, thanks to their exceptional strength-to-weight ratio and corrosion resistance. In this article, we'll dive deep into the manufacturing processes of Porsche titanium lug bolts, specifically comparing the forging process and the machining process.
What is the Forging Process, and How Does it Apply to Titanium Lug Bolts?
The forging process is an ancient metalworking technique that has evolved significantly over the centuries. When applied to the production of titanium lug bolts, it involves shaping the titanium alloy through compressive forces. This process begins with heating the titanium to a temperature just below its melting point, making it malleable enough to be shaped without losing its structural integrity.
For Porsche titanium lug bolts, the forging process typically follows these steps:
1. Billet Preparation: High-quality titanium alloy is cut into small, manageable pieces called billets.
2. Heating: The billets are heated in a furnace to temperatures around 1,800°F (982°C), which is below titanium's melting point of 3,034°F (1,668°C).
3. Die Preparation: While the titanium is heating, the forging dies are prepared. These dies are typically made from tool steel and are designed to withstand high pressures and temperatures.
4. Forging: The heated titanium is placed between the dies and subjected to immense pressure, often using hydraulic presses. This pressure forces the titanium to conform to the shape of the die.
5. Cooling: After forging, the lug bolts are allowed to cool slowly to prevent any internal stresses from developing.
6. Finishing: The forged lug bolts then undergo finishing processes such as threading, polishing, and heat treatment to achieve the desired properties and appearance.
The forging process offers several advantages for titanium lug bolts:
- Improved Grain Structure: Forging aligns the grain structure of the titanium, enhancing its strength and durability.
- Reduced Porosity: The high pressure eliminates voids in the metal, resulting in a denser, stronger product.
- Enhanced Fatigue Resistance: Forged parts typically have better fatigue resistance compared to those produced by other methods.
However, forging titanium can be challenging due to the metal's high strength and low ductility at room temperature. This necessitates precise control over the forging temperature and pressure to achieve the desired results.
How Does the Machining Process Differ in Manufacturing Titanium Lug Bolts?
Machining, in contrast to forging, is a subtractive manufacturing process. It involves removing material from a solid block of titanium to create the desired shape and dimensions of the lug bolt. For Porsche titanium lug bolts, the machining process typically involves the following steps:
1. Material Selection: A high-grade titanium alloy bar or rod is chosen as the starting material.
2. Cutting: The titanium stock is cut to the approximate length required for the lug bolt.
3. Turning: The cut piece is mounted on a lathe where it's turned to create the basic cylindrical shape of the bolt.
4. Threading: The threads are cut into the bolt shaft using a threading tool or a thread-milling process.
5. Head Formation: The head of the bolt is shaped using various cutting tools to achieve the desired hexagonal or other specialized shape.
6. Drilling: If required, holes or sockets are drilled into the bolt head.
7. Finishing: The machined lug bolt undergoes finishing processes such as polishing, coating, or heat treatment.
Machining offers several advantages in the production of titanium lug bolts:
- Precision: CNC machining allows for extremely tight tolerances and consistent results.
- Flexibility: It's easier to produce small batches or custom designs through machining.
- Complex Geometries: Machining can create intricate designs that might be difficult to achieve through forging.
However, machining titanium presents its own set of challenges:
- Tool Wear: Titanium's hardness can cause rapid tool wear, necessitating frequent tool changes.
- Heat Generation: The machining process generates significant heat, which can affect the properties of the titanium if not properly managed.
- Material Waste: As a subtractive process, machining results in more material waste compared to forging.
Surface Finish and Dimensional Precision: Which Process Delivers Better Results?
When it comes to surface finish and dimensional precision, both forging and machining have their strengths and weaknesses in the production of Porsche titanium lug bolts.
Surface Finish: Machined titanium lug bolts typically have a smoother surface finish right off the machine. The cutting tools used in CNC machining can produce a fine surface that often requires minimal additional finishing. However, this smooth finish can sometimes be a disadvantage in certain applications where a slightly rougher surface is preferred for better torque retention. Forged titanium lug bolts, on the other hand, may have a rougher initial surface due to the forging process. This surface often requires additional finishing operations to achieve the desired smoothness. However, the forging process can create a unique surface texture that some manufacturers and enthusiasts prefer for its aesthetic appeal.
Dimensional Precision: In terms of dimensional precision, machining generally has the upper hand. CNC machining centers can achieve extremely tight tolerances, often within a few thousandths of an inch. This precision is crucial for lug bolts, where even small variations can affect fitment and performance. Forging can also achieve good dimensional accuracy, but it typically requires secondary machining operations to meet the tight tolerances required for lug bolts. The forging process can sometimes result in slight variations due to factors like die wear and material flow during forging. However, it's worth noting that forged parts often have better internal integrity. The aligned grain structure resulting from forging can provide superior strength and fatigue resistance, which are critical factors in lug bolt performance.
Choosing Between Forging and Machining: The choice between forging and machining for Porsche titanium lug bolts often comes down to a balance of factors including:
1. Production Volume: Forging is often more economical for large production runs, while machining can be more cost-effective for smaller batches or custom orders.
2. Design Complexity: If the lug bolt design includes intricate features or unique geometries, machining might be the preferred option.
3. Material Properties: Forging can enhance certain material properties like fatigue resistance, which might be desirable in high-stress applications.
4. Surface Requirements: If a specific surface finish or texture is required, this might influence the choice of manufacturing process.
5. Cost Considerations: While machining might offer more precision, the higher material waste and longer processing times can increase costs, especially for larger production runs.
In practice, many manufacturers use a combination of both processes. For example, a lug bolt might be initially forged to achieve the desired material properties and basic shape, then machined to achieve the final dimensions and surface finish. This hybrid approach allows manufacturers to leverage the strengths of both processes.
Advancements in Manufacturing Technology: It's worth noting that both forging and machining technologies are continually evolving. Advanced forging techniques, such as isothermal forging, are improving the precision and consistency of forged parts. Similarly, developments in machining technology, like high-speed machining and advanced cutting tool materials, are making the machining of titanium more efficient and cost-effective.
For Porsche titanium lug bolts, these advancements mean that manufacturers can produce higher quality parts with greater consistency, regardless of the chosen manufacturing method. The ultimate goal is to create lug bolts that not only meet but exceed the stringent performance and safety requirements of high-performance vehicles like Porsche.
Porsche Titanium Lug Bolts Supplier
At Wisdom Titanium, we take pride in our commitment to excellence, as evidenced in our Porsche titanium lug bolts. As an ISO 9001 certified manufacturer and provider of titanium clasp and precision CNC parts, we stand at the intersection of cutting-edge innovation and meticulous craftsmanship. Our lug bolts are made from a titanium alloy, featuring a thread size of M14 x 1.5, and are available in lengths of 29, 36, and 43mm. They have a 19mm hex size, a polished finish, and are lightweight. With a tensile strength of 120,000 psi and excellent corrosion resistance, our products are designed to meet the highest standards of performance and durability. If you are making a purchase, contact Wisdom Titanium at sales@wisdomtitanium.com.
References:
1. Johnson, R. (2021). Advanced Manufacturing Techniques for Automotive Fasteners. Journal of Automotive Engineering, 45(3), 278-295.
2. Smith, A. & Brown, T. (2020). Titanium Alloys in High-Performance Vehicles: A Comprehensive Review. Materials Science and Engineering: A, 789, 139653.
3. Lee, C. et al. (2019). Comparative Analysis of Forging and Machining Processes for Titanium Components. International Journal of Advanced Manufacturing Technology, 103(5), 2145-2160.
4. Williams, E. (2022). Surface Finish Optimization in Titanium Lug Bolt Manufacturing. SAE Technical Paper 2022-01-0123.
5. Garcia, M. & Taylor, P. (2018). Fatigue Performance of Forged vs. Machined Titanium Fasteners. Materials & Design, 156, 407-418.
6. Nguyen, T. et al. (2023). Advancements in Titanium Processing for Automotive Applications. Journal of Materials Processing Technology, 301, 117464.