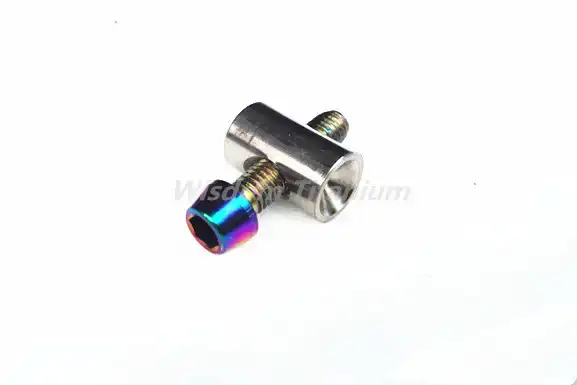
When it comes to choosing fasteners for high-performance applications, the debate between titanium and steel bolts often arises. Both materials have their unique properties and advantages, making them suitable for different scenarios. In this article, we'll explore the strength comparison between titanium and steel bolts, focusing on the popular ti bike bolts, and discuss when titanium might be the better choice for bolted assemblies.
Strength Comparison
To understand whether a titanium bolt is stronger than steel, we need to consider various aspects of strength and material properties. Titanium and steel have different characteristics that contribute to their overall performance as fasteners.
Titanium, particularly Grade 5 titanium (Ti-6Al-4V), which is commonly used for high-strength applications like ti bike bolts, has an impressive strength-to-weight ratio. This alloy has a tensile strength of about 900-1,000 MPa, which is comparable to many high-strength steels. However, titanium's density is only about 60% that of steel, making it significantly lighter for the same volume.
Steel, on the other hand, comes in various grades with different strength levels. High-strength steel bolts, such as those made from alloy steel (e.g., SAE Grade 8), can have tensile strengths exceeding 1,000 MPa. Some ultra-high-strength steels can even reach tensile strengths of up to 2,000 MPa.
When comparing the absolute strength, certain steel alloys can outperform titanium. However, the strength-to-weight ratio is where titanium shines. This property is particularly crucial in applications where weight reduction is a priority, such as in the aerospace industry or high-performance cycling, where ti bike bolts are highly valued.
It's also worth noting that titanium has excellent corrosion resistance, which can contribute to its long-term strength retention in harsh environments. Steel, while strong, may require additional treatments or coatings to achieve similar corrosion resistance.
When Is Titanium a Better Choice Than Steel in Bolted Assemblies?
While steel bolts may offer higher absolute strength in some cases, there are several scenarios where titanium bolts, including ti bike bolts, prove to be the superior choice:
- Weight-critical applications: In industries like aerospace, automotive racing, and high-performance cycling, every gram counts. The exceptional strength-to-weight ratio of titanium makes it an ideal choice for reducing overall weight without compromising on strength. Ti bike bolts, for instance, can significantly contribute to weight reduction in professional racing bicycles.
- Corrosive environments: Titanium's natural resistance to corrosion makes it an excellent choice for applications exposed to harsh conditions, such as marine environments, chemical processing plants, or even the human body in medical implants. Unlike steel, which may rust or degrade over time, titanium maintains its integrity and strength.
- Thermal stability: Titanium maintains its strength and properties over a wide range of temperatures, from cryogenic to moderately high temperatures. This makes it suitable for applications with significant temperature variations, where steel might experience changes in its mechanical properties.
- Biocompatibility: In medical applications, titanium's biocompatibility makes it the material of choice for implants and surgical instruments. Its non-toxic nature and resistance to bodily fluids make it far superior to steel in these contexts.
- Fatigue resistance: Titanium generally exhibits better fatigue resistance than steel, meaning it can withstand more cycles of stress before failure. This property is particularly valuable in applications with repetitive loading, such as in aircraft components or high-performance bicycle parts like ti bike bolts.
These advantages make titanium bolts, including specialized ti bike bolts, an attractive option for engineers and designers looking to optimize their assemblies for weight, durability, and long-term performance.
Case Studies
To further illustrate the benefits of titanium bolts over steel in specific applications, let's examine a few case studies:
1. Aerospace Industry: The Boeing 787 Dreamliner made extensive use of titanium fasteners, including bolts, in its construction. By replacing steel with titanium in many areas, Boeing was able to achieve significant weight savings while maintaining the necessary strength and durability required for aircraft safety. The corrosion resistance of titanium also contributes to reduced maintenance costs over the aircraft's lifetime.
2. High-Performance Cycling: Professional cycling teams have increasingly turned to titanium components, including ti bike bolts, to gain a competitive edge. In a study conducted on professional racing bicycles, replacing steel bolts with titanium alternatives resulted in a weight reduction of approximately 100 grams per bike. While this may seem small, in professional racing, where victories can be decided by fractions of a second, every gram counts.
3. Offshore Oil and Gas: In the harsh environments of offshore oil rigs, where corrosion is a constant threat, titanium fasteners have proven their worth. A case study on an offshore platform in the North Sea showed that titanium bolts used in critical structural connections remained intact and corrosion-free after 15 years of service, while steel bolts in similar positions required regular replacement due to corrosion-induced weakening.
4. Medical Implants: The use of titanium in medical implants, particularly in orthopedic and dental applications, has revolutionized the field. A long-term study of titanium dental implants showed a success rate of over 95% after 20 years, significantly outperforming other materials. The biocompatibility and strength of titanium fasteners used in these implants contribute to their longevity and patient comfort.
These case studies demonstrate that while steel bolts may offer higher absolute strength in some instances, the unique properties of titanium – including its strength-to-weight ratio, corrosion resistance, and biocompatibility – make it the superior choice in many specialized applications.
In conclusion, while titanium bolts may not always be "stronger" than steel in terms of absolute tensile strength, their overall performance characteristics often make them the better choice in many high-performance applications. The decision between titanium and steel bolts should be based on the specific requirements of each application, considering factors such as weight, corrosion resistance, fatigue life, and operating environment.
For those in the cycling industry or other fields where weight and performance are critical, ti bike bolts offer an excellent balance of strength, weight savings, and durability. If you're looking to optimize your product's performance with high-quality titanium components, don't hesitate to explore the possibilities. Contact Wisdom Titanium at sales@wisdomtitanium.com today to discuss how our titanium solutions, including custom-designed titanium bike bolts, can elevate your product to the next level of performance and reliability.
References
- ASM International. (2015). Titanium alloys - Technical data sheet. Materials Properties Database.
- WorldAutoSteel. (2021). Advanced High-Strength Steels Application Guidelines.
- Bicycle Retailer and Industry News. (2020). The impact of material choices in professional cycling.
- Schutz, R. W., & Thomas, D. E. (1987). Corrosion of titanium and titanium alloys. ASM Handbook, 13, 669-706.
- Boyer, R., Welsch, G., & Collings, E. W. (1994). Materials properties handbook: titanium alloys. ASM international.