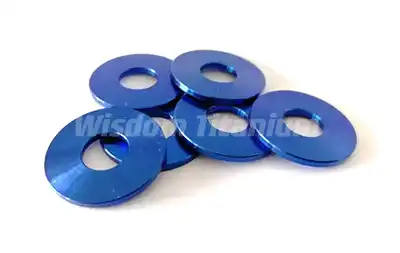
Titanium oversize washers are increasingly vital across various industries due to their remarkable strength, lightweight, and corrosion resistance. Made from titanium and its alloys, they are ideal for aerospace, marine engineering, chemical processing, and medical implants. Titanium's excellent strength-to-weight ratio and biocompatibility make it particularly suitable for applications where weight reduction is critical, like aircraft and automotive parts. Its exceptional corrosion resistance addresses material degradation and potential failures, especially in harsh environments. Understanding these properties helps engineers select materials and develop designs that ensure durability and reliability in demanding applications.
Impact Of Corrosive Environments
Titanium oversize washers are often employed in environments that would be highly corrosive to many other metals. These environments can include marine settings with high salt content, industrial processes involving acidic or alkaline solutions, and even the human body in the case of medical implants. Each of these environments presents unique challenges to the integrity of metal components.
In marine environments, the high chloride content of seawater can be particularly aggressive towards many metals, causing rapid corrosion through processes like pitting or crevice corrosion. However, titanium exhibits excellent resistance to seawater corrosion due to its ability to form a stable, protective oxide layer. This layer, primarily composed of titanium dioxide (TiO2), forms spontaneously when titanium is exposed to oxygen and provides a barrier against further corrosion.
Acidic environments, such as those found in chemical processing plants or certain natural settings like hot springs, can rapidly degrade many metals through chemical reactions that dissolve the metal surface. Titanium, however, maintains its corrosion resistance in most acidic environments due to the stability of its protective oxide layer in a wide range of pH levels. This resistance extends to many organic acids as well, making titanium washers suitable for use in food processing and pharmaceutical industries.
Alkaline environments, while less commonly associated with severe corrosion, can still pose challenges for many metals. Titanium's oxide layer remains stable in alkaline conditions, providing continued protection. This makes titanium washers suitable for applications in industries such as paper and pulp processing, where alkaline chemicals are commonly used.
The corrosion resistance mechanism of titanium is primarily attributed to its ability to form a passive oxide layer. When exposed to oxygen, titanium rapidly forms a thin, adherent oxide film on its surface. This film, typically only a few nanometers thick, is highly stable and self-healing. If the film is damaged mechanically, it quickly reforms in the presence of oxygen or water, providing continuous protection.
The stability of this oxide layer is due to the high affinity of titanium for oxygen and the nature of the oxide itself. Titanium dioxide is a ceramic material with high chemical stability. It adheres tightly to the underlying metal, preventing further oxidation and acting as a barrier against corrosive species in the environment.
Furthermore, the oxide layer on titanium is amphoteric, meaning it is stable in both acidic and alkaline environments. This property contributes to titanium's broad range of corrosion resistance across different pH levels, making it suitable for diverse applications where other metals might fail.
Surface Treatment Technology
While titanium naturally forms a protective oxide layer, various surface treatment technologies can be employed to enhance its corrosion resistance further. These treatments can be particularly beneficial for titanium oversize washers used in extremely aggressive environments or where an extra margin of safety is required.
One of the most common chemical treatments for titanium is anodizing. This electrochemical process artificially thickens and modifies the natural oxide layer on the titanium surface. Anodizing can produce oxide layers of varying thicknesses and compositions, depending on the process parameters. These anodized layers not only improve corrosion resistance but can also enhance wear resistance and provide a range of colors for aesthetic or identification purposes.
The anodizing process typically involves immersing the titanium washer in an electrolyte solution and applying an electrical current. The composition of the electrolyte and the voltage used can be varied to produce different types of oxide layers. For instance, thin film anodizing produces a transparent oxide layer that enhances corrosion resistance without significantly changing the dimensions of the washer. Thicker oxide layers can provide even greater protection but may affect the washer's dimensions and need to be accounted for in the design.
Another chemical treatment that can enhance corrosion resistance is passivation. This process involves removing surface contaminants and promoting the formation of a more stable oxide layer. Passivation typically involves cleaning the titanium surface and then exposing it to an oxidizing acid, such as nitric acid. This treatment can be particularly effective in removing iron contamination, which can impair titanium's natural corrosion resistance.
In addition to chemical treatments, coating technologies can also be applied to titanium oversize washers to provide enhanced corrosion protection. While titanium itself is highly corrosion-resistant, coatings can offer additional benefits in certain applications.
Polymer coatings, such as polytetrafluoroethylene (PTFE) or polyetheretherketone (PEEK), can be applied to titanium washers to provide not only corrosion resistance but also improved lubricity and chemical resistance. These coatings can be particularly useful in applications where the washer may come into contact with aggressive chemicals or where reduced friction is desirable.
Ceramic coatings, such as titanium nitride (TiN) or chromium nitride (CrN), can be applied using physical vapor deposition (PVD) techniques. These coatings offer excellent hardness and wear resistance in addition to corrosion protection. They are often used in high-wear applications or where additional surface hardness is required.
It's important to note that while these surface treatments and coatings can enhance the performance of titanium washers, they also add complexity and cost to the manufacturing process. The choice of treatment should be carefully considered based on the specific requirements of the application and the environmental conditions the washer will face.
Conclusion
In the global market for titanium components, including oversize washers, Chinese manufacturers have become significant players. One such company making strides in this field is Wisdom Titanium Company. They specialize in custom-designed titanium washers, catering to the specific needs of various industries that require high-performance, corrosion-resistant fasteners. For those in the market for titanium oversize washers and considering various manufacturers, Wisdom Titanium Company invites potential customers to reach out to them at sales@wisdomtitanium.com.
References
1. Lutjering, G., & Williams, J. C. (2007). Titanium (2nd ed.). Springer-Verlag Berlin Heidelberg.
2. ASM International. (2005). ASM Handbook, Volume 13B: Corrosion: Materials.
3. Schutz, R. W., & Thomas, D. E. (1987). Corrosion of titanium and titanium alloys. ASM Handbook, 13, 669-706.
4. Donachie, M. J. (2000). Titanium: A Technical Guide (2nd ed.). ASM International.
5. Davis, J. R. (Ed.). (2001). Surface Engineering for Corrosion and Wear Resistance. ASM International.