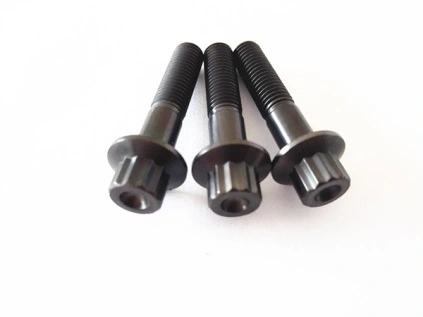
How Durable Are Titanium Alloy Bolts?
As a mechanical engineer specializing in materials science, I have often been asked about the durability of titanium alloy bolts. In this article, I will delve into the properties of titanium alloys, their suitability for bolt applications, and their durability under various conditions.
Understanding Titanium Alloys
Titanium combinations are a gather of materials known for their remarkable strength-to-weight proportion, erosion resistance, and biocompatibility. These combinations are essentially composed of titanium along with other components like aluminum, vanadium, or nickel, which are included to improve particular properties.
Properties of Titanium Alloys:
Strength and Lightweight: Titanium amalgams are eminent for their tall strength-to-weight proportion, making them perfect for applications where weight decrease is basic without compromising quality. This characteristic makes titanium combinations especially appealing for aviation and car industries.
Corrosion Resistance: Titanium amalgams show great erosion resistance, particularly in forceful situations such as seawater and chemical handling. This property is due to the arrangement of a defensive oxide layer on the surface of the fabric, which avoids assist corrosion.
Biocompatibility: Titanium combinations are biocompatible, meaning they are well-tolerated by the human body and are commonly utilized in restorative inserts such as fake joints and dental implants.
Suitability for Jolt Applications:
The properties of titanium combinations make them appropriate for different jolt applications, particularly in businesses where lightweight, erosion resistance, and tall quality are basic variables. A few particular applications include:
Aerospace: Titanium jolts are broadly utilized in aviation applications due to their lightweight nature and tall quality. They offer assistance decrease the in general weight of air ship, which is pivotal for fuel proficiency and performance.
Marine: In marine situations where erosion is a critical concern, titanium jolts offer great resistance to seawater erosion, making them perfect for marine structures and equipment.
Medical: Titanium jolts discover applications in restorative gadgets and inserts where biocompatibility is basic. They are frequently utilized in orthopedic surgeries for bone obsession due to their quality and compatibility with the human body.
Durability under Various Conditions:
Titanium alloy bolts exhibit exceptional durability under various conditions, but their performance can be influenced by factors such as temperature, stress, and environment:
Temperature: Titanium alloys maintain their strength and integrity at high temperatures, making them suitable for applications in aerospace engines and exhaust systems.
Stress: Titanium alloys have excellent fatigue resistance, meaning they can withstand repeated loading and unloading without failure. This property is crucial for bolt applications where cyclic loading is common.
Environment: The corrosion resistance of titanium alloys ensures their durability in harsh environments such as marine and chemical processing facilities. However, exposure to certain chemicals or high concentrations of oxygen at elevated temperatures can compromise their corrosion resistance.
Factors Affecting Durability
The durability of them can be influenced by various factors, including:
Material Composition: The specific composition of the titanium alloy used for the bolts can significantly impact their durability. Different alloying elements, such as aluminum, vanadium, or nickel, can alter the mechanical properties, corrosion resistance, and overall performance of the bolts.
Manufacturing Process: The manufacturing method and quality control measures employed during the production of them can affect their microstructure, integrity, and mechanical properties. Proper heat treatment and machining techniques are crucial for ensuring the bolts meet the required standards for durability.
Environmental Conditions: The operating environment in which the bolts are utilized plays a critical role in their durability. Factors such as temperature, humidity, exposure to chemicals, and presence of corrosive agents can affect the performance and longevity of titanium alloy bolts. Proper material selection and surface treatments may be necessary to enhance corrosion resistance in challenging environments.
Loading Conditions: The magnitude and type of loads applied to the bolts, including tension, compression, shear, and cyclic loading, can impact their fatigue strength and durability. Understanding the intended application and designing the bolts to withstand the expected loads is essential for ensuring long-term performance.
Surface Protection: Surface treatments such as coatings, plating, or anodizing can provide additional protection against corrosion and wear, thereby improving the durability of them. These treatments can enhance the surface hardness, lubricity, and resistance to environmental degradation.
Installation and Maintenance: Proper installation procedures, including torque specifications and preload requirements, are critical for ensuring the integrity and durability of them. Regular inspection and maintenance practices can help identify potential issues such as loosening, corrosion, or fatigue cracking, allowing for timely corrective actions to be taken.
Material Degradation: Over time, they may experience degradation mechanisms such as corrosion, hydrogen embrittlement, or creep, which can compromise their mechanical properties and structural integrity. Monitoring and preventive measures, such as corrosion inhibitors or periodic replacements, may be necessary to mitigate these degradation effects and maintain the durability of the bolts.
Durability in Real-world Applications
Aerospace Applications: Titanium alloy bolts are commonly used in aerospace applications due to their lightweight nature, high strength, and corrosion resistance. In aircraft structures, these bolts may be subjected to cyclic loading during flight, as well as exposure to varying temperatures, humidity levels, and atmospheric conditions. The durability of these bolts is crucial for ensuring the structural integrity of critical components such as wings, fuselage, and engine assemblies. Proper material selection, surface treatments, and fatigue analysis are essential for designing them that can withstand the demanding conditions encountered in aerospace environments.
Marine Environments: In marine applications, they are employed in structures exposed to seawater, such as ship hulls, offshore platforms, and marine equipment. The corrosive nature of seawater poses a significant challenge to the durability of metallic components, including bolts. Titanium alloys offer excellent resistance to seawater corrosion, making them well-suited for such applications. However, factors such as galvanic corrosion from dissimilar metals, biofouling, and mechanical loading from waves and currents can still affect the performance of titanium alloy bolts over time. Proper design considerations, material compatibility assessments, and corrosion protection measures are essential for ensuring the long-term durability of bolts in marine environments.
Biomedical Implants: They are used in medical implants such as orthopedic screws, plates, and dental implants due to their biocompatibility and mechanical properties. In biomedical applications, the durability of these bolts is critical for ensuring the stability and longevity of the implants within the human body. Factors such as stress shielding, osseointegration, and tissue response can influence the performance of them in vivo. Proper design optimization, surface modifications to promote bone ingrowth, and biocompatibility testing are necessary to ensure the durability and reliability of implants over extended periods of time.
Automotive and Racing: They find applications in automotive and racing industries where lightweight components and high-performance fasteners are required. In racing cars, for example, titanium bolts are used to secure critical components such as suspension systems, engine mounts, and chassis components. These bolts must withstand high levels of mechanical loading, vibration, and thermal cycling while minimizing weight. Durability considerations include fatigue strength, thermal expansion coefficients, and compatibility with other materials in the assembly. Advanced engineering techniques such as finite element analysis (FEA) and materials testing are employed to optimize the design and durability of it in automotive applications.t
In conclusion
In conclusion, titanium alloy bolts offer exceptional durability due to their high strength, corrosion resistance, and lightweight properties. When properly designed, processed, and installed, titanium bolts can provide reliable performance in a wide range of applications, from aerospace and automotive to marine and industrial settings. Their impressive durability makes them a preferred choice for demanding environments where reliability and performance are paramount.
If you want to know more about it, please contact us: sales@wisdomtitanium.com.