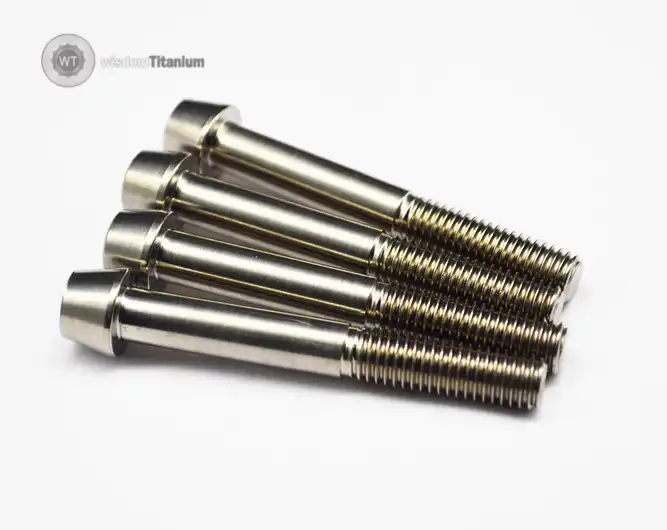
Are Ti64 Bolts Durable?
Introduction As an engineer deeply engaged in the world of materials science and engineering, I have often been asked about the durability of Ti64 bolts. Titanium alloy Ti64, also known as Ti-6Al-4V, is a popular choice in various industries due to its exceptional strength-to-weight ratio and corrosion resistance. However, when it comes to the durability of them, there are several factors to consider. In this article, I will delve into the scientific basis of Ti64 bolt durability, addressing key aspects such as material properties, fatigue behavior, and real-world applications.
Material Properties of Ti64 Bolts
Ti64 bolts, made from the titanium alloy Ti64, indeed possess remarkable material properties that make them highly desirable for various applications. Here's a breakdown of some of the key material properties of them:
Tall Quality: Ti64 jolts display tall malleable quality, which alludes to their capacity to withstand pulling or malleable powers without breaking. This property is significant for clasp like jolts, particularly in applications where they require to hold overwhelming loads or persevere noteworthy stress.
Fatigue Quality: Weakness quality is the capacity of a fabric to stand up to disappointment beneath cyclic stacking or rehashed push. Ti64 jolts illustrate great weariness quality, guaranteeing their unwavering quality and strength indeed beneath conditions of rehashed stacking and unloading.
Corrosion Resistance: Titanium combinations, counting Ti64, are known for their extraordinary erosion resistance. This property makes Ti64 jolts appropriate for utilize in situations where introduction to dampness, chemicals, or other destructive components is a concern. This erosion resistance contributes to the life span and unwavering quality of the jolts, especially in open air or unforgiving mechanical environments.
High Strength-to-Weight Proportion: One of the most noteworthy points of interest of Ti64 jolts is their noteworthy strength-to-weight proportion. Titanium has a moo thickness compared to numerous other metals, counting steel, whereas still advertising amazing quality. This implies Ti64 jolts can give the same level of auxiliary judgment and execution as heavier steel jolts but with essentially less weight. This characteristic is particularly important in aviation, car, and other weight-sensitive applications, where lessening weight without compromising quality is critical.
Enhanced Mechanical Properties: The nearness of aluminum and vanadium in the Ti64 combination contributes to its upgraded mechanical properties. Aluminum moves forward the alloy's quality and hardness, whereas vanadium upgrades its durability and resistance to weakness. These alloying components play a pivotal part in optimizing the execution of Ti64 jolts in requesting applications.
Overall, Ti64 jolts offer a compelling combination of quality, strength, and erosion resistance, making them a favored choice for a wide extend of mechanical and building applications where unwavering quality and execution are foremost.
Fatigue Behavior of Ti64 Bolts
The fatigue behavior of Ti64 bolts is indeed a crucial aspect to consider for ensuring their long-term reliability and performance, particularly in applications subjected to cyclic loading or vibration. Here's a closer look at the factors influencing the fatigue behavior of them and how their unique characteristics contribute to superior fatigue resistance:
Material Microstructure: The microstructure of Ti64, characterized by the presence of both α (alpha) and β (beta) phases, plays a significant role in determining its fatigue behavior. This dual-phase microstructure allows for efficient stress distribution and crack propagation resistance, contributing to enhanced fatigue resistance. The distribution and morphology of these phases can be tailored through various heat treatment processes to optimize fatigue performance for specific applications.
Surface Finish: The surface finish of them can influence their fatigue behavior by affecting factors such as stress concentration and crack initiation. A smooth surface finish can help minimize stress concentrations and reduce the likelihood of fatigue crack initiation, thereby improving fatigue resistance. Additionally, surface treatments or coatings may be applied to further enhance corrosion resistance and fatigue performance in aggressive environments.
Oxide Layer Formation: Titanium alloys, including Ti64, have a natural affinity for oxygen, which leads to the formation of a protective oxide layer on the surface. This oxide layer acts as a barrier, providing corrosion resistance and reducing the susceptibility to fatigue crack initiation. The presence of this oxide layer is particularly beneficial in applications exposed to harsh or corrosive environments, where it helps maintain the integrity of the bolt over extended periods.
Loading Conditions: The fatigue strength of them can also be influenced by factors such as loading conditions, including the magnitude and frequency of cyclic loading, as well as the presence of any residual stresses. Understanding the specific loading conditions and designing bolts accordingly can help optimize their fatigue performance and ensure long-term reliability.
Real-World Applications of Ti64 Bolts
The real-world applications of Ti64 bolts underscore their versatility and reliability across various industries:
Aerospace: They play a crucial role in aircraft structures, engines, and landing gear systems. Their lightweight yet durable properties contribute to fuel efficiency, allowing aircraft to carry heavier payloads while meeting safety standards. Moreover, their corrosion resistance ensures longevity in harsh environmental conditions, making them essential components in the aerospace industry.
Automotive: In high-performance vehicles, they are prized for their ability to reduce weight without compromising strength. By utilizing these bolts in critical components like engine mounts, suspension systems, and chassis structures, automotive manufacturers can enhance overall performance, agility, and fuel efficiency. Additionally, their resistance to corrosion makes them suitable for use in various automotive environments.
Medical: They find extensive use in orthopedic implants due to their biocompatibility and corrosion resistance. In procedures such as fracture fixation and joint replacements, these bolts offer excellent strength-to-weight ratios and minimize the risk of adverse reactions within the human body. Their durability and compatibility with medical imaging techniques also contribute to successful surgical outcomes and patient recovery.
Sporting Goods: Ti64 bolts are essential components in sporting goods, particularly in bicycles, racing motorcycles, and other performance-oriented equipment. Their lightweight design enhances agility and speed, making them ideal for competitive sports where every ounce matters. Additionally, their corrosion resistance ensures durability, even in challenging outdoor environments.
In each of these applications, they demonstrate exceptional performance under demanding conditions, showcasing their reliability and effectiveness across diverse industries. Their unique combination of strength, lightness, and corrosion resistance continues to drive innovation and advancements in technology, benefiting various sectors and end-users alike.
Conclusion
In conclusion, Ti64 bolts exhibit exceptional durability due to their unique material properties, fatigue resistance, and performance in real-world applications. The combination of titanium, aluminum, and vanadium in Ti64 alloy provides high strength, lightness, and corrosion resistance, making it suitable for a wide range of industries and applications. As a professional in the field of materials science and engineering, I can confidently attest to the durability and reliability of Ti64 bolts for critical applications where performance is paramount.
If you want to know more about it, please contact us: sales@wisdomtitanium.com.
References:
- Boyer, R. (1996). An overview on the use of titanium in the aerospace industry. Materials Science and Engineering: A, 213(1-2), 103-114.
- ASTM International. (2019). Standard Specification for Titanium and Titanium Alloy Bars and Billets. ASTM B348 / B348M - 19.
- ASM International. (2001). ASM Handbook: Volume 2, Properties and Selection: Nonferrous Alloys and Special-Purpose Materials. ASM International.
- Lütjering, G., & Williams, J. C. (2007). Titanium (2nd ed.). Springer.