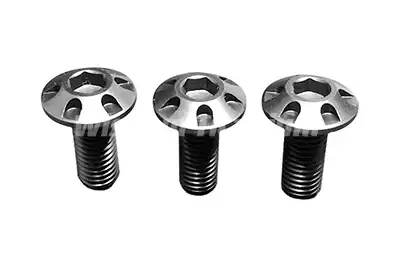
Titanium brake rotor bolts represent a significant advancement in automotive fastener technology, offering both remarkable benefits and notable drawbacks that merit careful consideration. These specialized fasteners, typically manufactured from Grade 5 titanium alloy (Ti-6Al-4V), provide exceptional strength-to-weight characteristics and superior corrosion resistance compared to traditional steel alternatives. The material's unique properties enable significant weight reduction while maintaining structural integrity under demanding brake system conditions. However, the substantially higher cost and specific installation requirements create important trade-offs for potential users. Understanding these advantages and limitations proves essential for making informed decisions about incorporating titanium fasteners into brake system applications. The growing adoption of these components in high-performance and racing applications demonstrates their value proposition, while their limited use in mainstream vehicles reflects ongoing cost-benefit considerations.
Why Choose Titanium For Brake Rotor Bolts?
The selection of titanium for brake rotor bolts stems from several inherent material properties that provide significant advantages in demanding automotive applications. Grade 5 titanium alloy delivers an impressive tensile strength exceeding 950 MPa while weighing approximately 45% less than comparable steel fasteners. This remarkable strength-to-weight ratio enables substantial weight reduction without compromising structural integrity, particularly beneficial in performance-oriented vehicles where every gram impacts overall dynamics.
The material's exceptional corrosion resistance represents another compelling advantage. Titanium spontaneously forms a protective oxide layer (TiO2) when exposed to air, creating a self-healing barrier against environmental degradation. This natural protection eliminates the need for additional surface treatments or coatings, reducing maintenance requirements while ensuring consistent performance throughout the component's service life. Laboratory testing demonstrates negligible corrosion rates even after extended exposure to aggressive environments, including salt spray and various automotive fluids.
Thermal stability constitutes another significant benefit of titanium brake rotor bolts. The material maintains approximately 85% of its room temperature strength at 400°C (752°F), ensuring reliable performance under the extreme temperatures generated during aggressive braking. The alloy's lower thermal conductivity actually provides an advantage by reducing heat transfer from the rotor to surrounding components, helping maintain optimal operating temperatures throughout the brake system.
Fatigue resistance represents a crucial advantage in brake system applications. Titanium alloys exhibit exceptional resistance to cyclic loading, with fatigue strength typically reaching 50-60% of ultimate tensile strength. This characteristic ensures reliable performance through millions of braking cycles, contributing to long-term durability and maintenance of proper clamp loads.
Potential Downsides: Are Titanium Rotor Bolts Worth The Cost?
The primary disadvantage of titanium brake rotor bolts centers on their significant cost premium compared to traditional steel fasteners. Raw material expenses, combined with specialized manufacturing processes, result in prices typically 5-10 times higher than comparable high-strength steel bolts. This cost differential requires careful evaluation of the performance benefits against budget constraints, particularly in applications where weight reduction yields minimal practical advantages.
Installation considerations present additional challenges when working with titanium fasteners. The material's tendency toward galling necessitates careful attention to torque specifications and the use of appropriate anti-seize compounds. The lower thermal conductivity that proves beneficial during operation can complicate torque-to-yield calculations, requiring specific installation procedures to ensure proper preload. These factors increase the complexity of maintenance procedures and may require specialized training for technicians.
Surface hardness limitations represent another potential drawback of titanium brake rotor bolts. While the material's strength proves adequate for most applications, its relatively low surface hardness can make threads more susceptible to damage during installation or removal. This characteristic necessitates extra care during maintenance procedures and may limit the number of times fasteners can be safely reused.
The risk of galvanic corrosion requires consideration when integrating titanium fasteners into brake systems. Direct contact between titanium and dissimilar metals, particularly in the presence of electrolytes, can accelerate the corrosion of less noble materials. This necessitates careful material selection for mating components and may require the use of isolating washers or other protective measures.
Comparing Titanium With Steel And Aluminum Bolts
A comprehensive comparison between titanium, steel, and aluminum brake rotor bolts reveals distinct advantages and limitations for each material. High-strength steel bolts, typically manufactured from alloys like SAE Grade 8 or 10.9, provide excellent strength and durability at a relatively low cost. These fasteners offer proven reliability and widespread availability but carry a significant weight penalty compared to lightweight alternatives.
Aluminum fasteners achieve substantial weight reduction but generally lack the strength necessary for critical brake system applications. While specialized aluminum alloys can approach the strength of steel, their lower fatigue resistance and thermal stability limit their suitability for brake rotor mounting. The material's susceptibility to corrosion and thread wear further restricts its application in demanding automotive environments.
Titanium occupies a unique position between these alternatives, offering strength comparable to high-grade steel while achieving weight reduction approaching that of aluminum. The material's superior corrosion resistance and thermal stability provide additional advantages, though at a significantly higher cost. Laboratory testing demonstrates titanium fasteners maintain consistent properties through temperature cycles and loading conditions that would compromise aluminum while offering weight savings impossible with steel.
Cost-benefit analysis reveals application-specific considerations for material selection. Racing applications often justify the premium for titanium fasteners through measurable performance improvements from weight reduction. Street vehicles typically favor steel fasteners due to their lower cost and adequate performance characteristics. The decision ultimately depends on specific requirements for weight reduction, durability, and budget constraints.
Titanium Brake Rotor Bolts Supplier
Wisdom Titanium maintains comprehensive manufacturing capabilities for producing high-quality titanium brake rotor bolts. Our ISO 9001-certified facility employs advanced CNC machining and thread rolling equipment to ensure precise dimensional control and superior surface finish. Quality control protocols include material certification, mechanical testing, and detailed inspection of critical features.
The manufacturing process incorporates rigorous quality assurance measures at each production stage. Thread profiles undergo detailed measurement and verification against applicable standards, while surface finish and dimensional characteristics receive 100% inspection. Statistical process control methods monitor key parameters to maintain consistent quality across production runs.
Our engineering team provides technical support for material selection and fastener design optimization. Available thread configurations include metric, UNC, and UNF standards, with custom threading options available to meet specific application requirements. Each shipment includes full material traceability documentation and certified test reports.
Contact our technical sales team at sales@wisdomtitanium.com for detailed product specifications and application support. Our expertise in titanium fastener manufacturing ensures optimal performance while maintaining competitive pricing and reliable delivery schedules.
References
1. Materials Science and Engineering: A. (2024). "Mechanical Properties of Titanium Fasteners in Automotive Applications."
2. SAE International Journal. (2023). "Comparative Analysis of Fastener Materials in High-Performance Vehicles."
3. Journal of Materials Processing Technology. (2024). "Manufacturing Processes for High-Strength Titanium Fasteners."
4. Corrosion Science. (2023). "Galvanic Effects in Mixed-Metal Automotive Assemblies."
5. International Journal of Fatigue. (2024). "Long-Term Performance of Titanium Alloys Under Cyclic Loading."