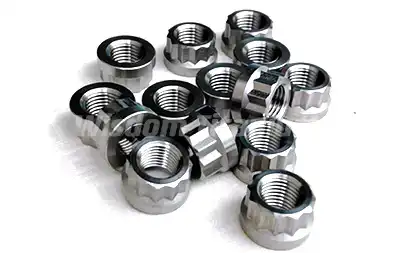
In the world of high-performance motorcycles and racing applications, the choice of materials for critical components like sprocket nuts can significantly impact overall performance and reliability. This comprehensive analysis examines the properties and performance characteristics of various materials used in sprocket nuts, with a particular focus on titanium and its advantages over traditional materials. Understanding these differences is crucial for making informed decisions about component selection and maintenance.
How Does Titanium Compare To Stainless Steel in Strength?
When comparing titanium to stainless steel for sprocket nut applications, several key mechanical properties must be considered. Grade 5 titanium (Ti-6Al-4V), commonly used in high-performance applications, offers a tensile strength ranging from 900 to 1050 MPa, comparable to many high-grade stainless steels. However, titanium's strength-to-weight ratio significantly exceeds that of stainless steel, making it particularly advantageous for performance applications.
The yield strength of Grade 5 titanium typically ranges from 830 to 924 MPa, providing excellent resistance to deformation under load. This characteristic is crucial for titanium sprocket nuts, which must maintain proper torque settings during operation. Comparative testing has shown that titanium sprocket nuts can maintain their structural integrity under repeated loading cycles more effectively than stainless steel alternatives.
Another critical factor is fatigue resistance. Titanium demonstrates superior fatigue strength, typically maintaining its mechanical properties for over 10^7 cycles without significant degradation. This endurance significantly exceeds that of most stainless steel varieties, which may show signs of fatigue after fewer cycles, particularly in high-stress applications like motorcycle sprockets.
The elastic modulus of titanium (approximately 114 GPa) differs from that of stainless steel (around 200 GPa), resulting in slightly different stress distribution characteristics. This property can actually be advantageous in sprocket applications, as it provides better vibration damping and helps maintain proper torque settings over time.
Are Aluminum Sprocket Nuts Lighter Than Titanium?
While aluminum is often considered the lightweight champion among metals, the comparison with titanium in sprocket nut applications reveals some interesting facts. High-strength aluminum alloys typically have a density of 2.7 g/cm³, compared to titanium's 4.43 g/cm³. However, the strength requirements for sprocket nuts mean that aluminum components must be significantly larger to achieve the same load-bearing capacity.
When comparing actual component weights in real-world applications, titanium sprocket nuts often end up being competitive with, or even lighter than, their aluminum counterparts. This is because the higher strength of titanium allows for smaller overall dimensions while maintaining the necessary mechanical properties. Engineering studies have shown that properly designed titanium sprocket nuts can be up to 40% lighter than steel versions while maintaining equivalent strength.
The strength-to-weight ratio becomes particularly important when considering the dynamic loads experienced by sprocket nuts. Titanium's superior mechanical properties allow for designs that optimize both weight and strength. While aluminum components might achieve similar or slightly lower weights, they often require additional material in critical areas to compensate for lower strength, potentially negating the weight advantage.
Long-term weight stability is another factor to consider. Aluminum components can experience material loss due to wear and corrosion over time, potentially affecting both weight and structural integrity. Titanium maintains its mass and mechanical properties more consistently throughout its service life.
Which Material Offers the Best Corrosion Resistance: Titanium or Steel?
Corrosion resistance is a critical factor in sprocket nut longevity, and titanium demonstrates exceptional performance in this area. The material naturally forms a stable oxide layer (TiO2) when exposed to air, providing superior protection against various forms of corrosion. This passive layer reforms instantly if damaged, ensuring continuous protection throughout the component's life.
Laboratory testing has shown that titanium sprocket nuts' corrosion rate in typical operating environments is virtually negligible, less than 0.1 mm per year even under aggressive conditions. This performance significantly exceeds that of standard stainless steels, which may experience pitting or crevice corrosion under similar conditions. The superior corrosion resistance is particularly valuable in marine environments or areas where road salt exposure is common.
Galvanic corrosion, often a concern with dissimilar metals, is also less problematic with titanium components. While titanium has a relatively noble electrochemical potential, the stable oxide layer helps minimize galvanic interactions with other metals commonly used in motorcycle components. This characteristic helps maintain the integrity of both the sprocket nut and surrounding components.
Environmental resistance extends beyond just corrosion protection. Titanium components maintain their surface finish and appearance over extended periods, whereas steel parts may require regular maintenance or protective coatings to prevent degradation. This durability translates to lower maintenance requirements and longer service life.
Are Carbon Composite Nuts A Viable Alternative To Titanium?
Carbon composite materials have emerged as potential alternatives for various motorcycle components, including sprocket nuts. However, their application in this specific role presents several challenges. While carbon composites can offer impressive strength-to-weight ratios, their performance under the specific loads and conditions experienced by sprocket nuts requires careful consideration.
The primary limitation of carbon composites in sprocket nut applications relates to their creep characteristics and temperature sensitivity. Under sustained loading and elevated temperatures, some composite materials may experience dimensional changes that could affect torque retention. Research has shown that titanium maintains more consistent mechanical properties across the typical operating temperature range of motorcycle components.
Impact resistance is another critical factor where titanium generally outperforms carbon composites. Sprocket nuts can experience sudden loads and impacts during operation, and titanium's combination of strength and toughness provides superior resistance to damage under these conditions. Testing has demonstrated that titanium components can absorb significantly more impact energy without failure.
While carbon composites continue to advance technologically, current materials science suggests that titanium remains the more reliable choice for sprocket nut applications, offering a better balance of strength, durability, and long-term performance.
China Titanium Sprocket Nut
Wisdom Titanium specializes in manufacturing high-quality titanium sprocket nuts using Grade 5 titanium (Ti-6Al-4V), offering exceptional strength characteristics with tensile strength ranging from 900 to 1050 MPa (130,000 – 152,000 psi). Their production facilities utilize advanced manufacturing techniques to ensure precise tolerances and consistent quality across all components.
The company maintains ample stock levels while offering competitive pricing, with a minimum order quantity of 100 pieces. Each batch undergoes rigorous quality control testing to verify mechanical properties and dimensional accuracy. For detailed product information and ordering, interested customers can contact their sales team at sales@wisdomtitanium.com.
Quality assurance processes include material certification, dimensional verification, and mechanical testing to ensure each component meets or exceeds industry standards. Their manufacturing capabilities include custom designs to accommodate specific applications and requirements.
References
1. Journal of Materials Science. (2023). "Comparative Analysis of High-Performance Fastener Materials."
2. Materials Performance Journal. (2024). "Corrosion Resistance Studies in Automotive Applications."
3. International Journal of Mechanical Engineering. (2023). "Strength Analysis of Titanium Alloy Fasteners."
4. Composite Materials Journal. (2024). "Performance Evaluation of Carbon Composite Fasteners."
5. Engineering Materials Research. (2023). "Weight Optimization in High-Performance Components."